Plastic moulding is an essential process in the manufacturing industry. But do you know how it works and what different type of plastic moulding methods are available? In this blog post, we will take a deep dive into the world of plastic moulding and explore everything you need to know about this critical manufacturing process.
In a nutshell, plastic moulding is the process of creating plastic parts by injecting molten plastic into a mould. The molten plastic then cools and hardens to form the desired shape. There are several types of plastic moulding methods available, including injection moulding, compression moulding, blow moulding, and rotational moulding. Each technique has its own advantages and limitations, and the different moulding processes may or may not be suitable for moulding a particular project depending on several factors, such as the complexity of the part, the material used, and the production volume required.
If you’re interested in learning more about plastic moulding and how it can benefit your manufacturing process, then keep reading! We’ll cover everything from the basics of plastic moulding to the different techniques available and their applications. And, to make sure that you’re getting the most accurate and trustworthy information possible, we’ll be referencing renowned subject matter experts in the field of plastic moulding throughout the post. So, without any further ado, let’s dive into the fascinating world of plastic moulding!
Plastic Moulding Methods
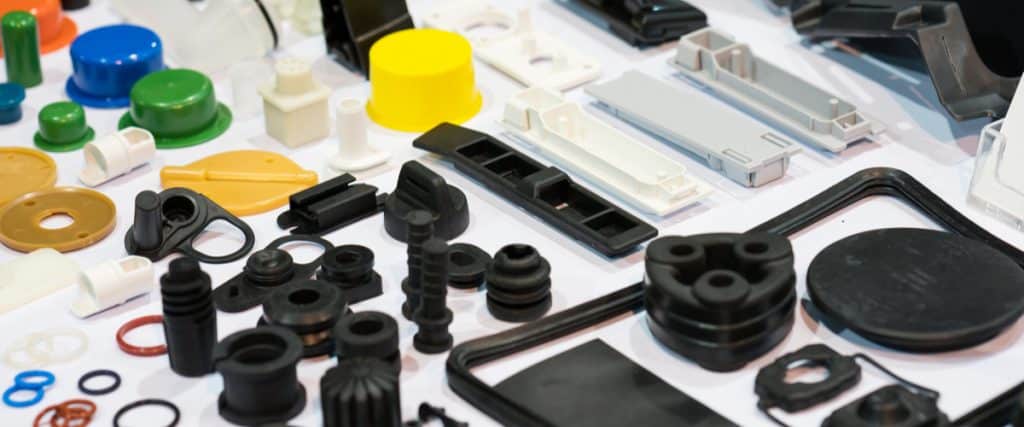
1. Plastic Moulding Methods: Injection Moulding
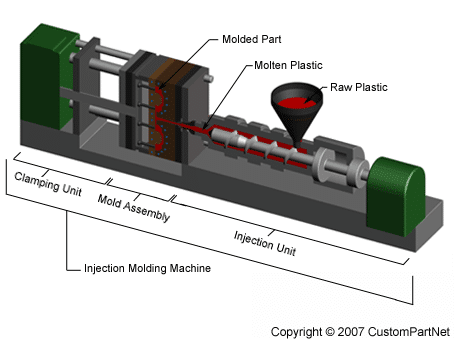
Injection moulding is one of the most common plastic moulding methods and it involves injecting molten plastic material into a mould cavity to create a particular shape or part. The process starts with feeding plastic pellets into a heated barrel (hopper), where they are melted and mixed.
Colour pigments or masterbatch can be added to the mix to give the moulded plastic a desired colour, while additives such as flame retardants or UV-stabilizers can be incorporated to enhance the plastic’s performance. Once the plastic is melted, it is injected into a mould under high pressure and then it is cooled solidifying into the desired shape.
This process was first developed in the 1870s, but it wasn’t until the 1940s that it became a widespread manufacturing technique, thanks greatly to World War II, which brought the demand for low-cost mass produced parts. This is when the first screw injection moulding machine was invented. Today, injection moulding is so common that it accounts for a significant percentage of all plastic products produced globally.
Injection moulding is commonly used for producing a wide range of products, including everything from automotive parts and packaging to toys and medical equipment.
The process can accommodate a wide range of materials. Some of the most common ones are polyethylene (PE), polypropylene (PP), polystyrene (PS), acrylonitrile-butadiene-styrene (ABS), polycarbonate (PC), nylon (PA), and more. Each plastic has its own unique properties, making it suitable for different applications. For example, ABS is commonly used for making automotive parts, while polycarbonate is often used for electronic housings due to its high impact resistance.
Pros and cons of Injection Moulding
Injection moulding is a highly versatile and efficient process, with high precision and repeatability. In fact, injection moulding can produce highly precise and consistent parts with a low margin of error, making it ideal for applications where dimensional accuracy is critical.
However, this process does have some design constraints. For example, parts need to be designed with a draft angle to allow them to be easily ejected from the mould, and wall thicknesses need to be more or less consistent to avoid surface defects like sink marks or short shots.
Tooling costs can be high depending on the size, material, and complexity of the moulds. So, for larger and more complex parts it may not be viable to run low volume production runs. Very often a cheaper “soft tool” (generally made from a softer steel or aluminium) is made to test the part before the design is signed off and the company invests in the full production tooling.
In terms of the material selection, injection moulding can use a wide range of plastics, however, there are some that cannot be used. For example, certain thermoset plastics (polymers that are irreversibly hardened by heat), such as epoxy resins or fiberglass cannot be injection moulded, well… at least with a typical injection moulding machine.
Examples of common products
A large portion of the products you may see in front of you in this moment, are probably made with this moulding process. Here are a few common examples:
- LEGO® bricks: These iconic plastic building blocks are made using injection moulding, allowing for the precise and consistent manufacturing of millions of pieces every day.
- Disposable razors: Many disposable razors are made using injection moulding, which allows for the efficient production of millions of identical parts.
- Bottle caps: The caps used on many types of bottles, such as water bottles and soda bottles, are often made using injection moulding because of the high volume and consistency needed for these parts.
- Computer mice: The outer shells for many computer mice are created using injection moulding, which allows to produce intricate shapes and details at a high volume.
- Automotive parts: Injection moulding is commonly used to create various automotive parts, including interior components, dashboard panels, and exterior trim pieces.
2. Plastic Moulding Methods: Compression Moulding
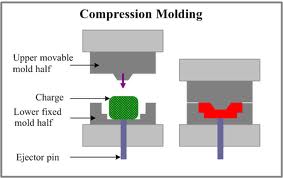
Compression moulding was first used as a manufacturing process in the early nineteenth century, when Thomas Hancock perfected the process to mould rubber. Compression moulding is a plastic moulding process that involves placing a heated plastic material in a heated mould cavity, then applying pressure to the material to force it to conform to the shape of the mould, a bit like Play-doh.
Today, compression moulding is used for a wide range of products, including electrical components, automotive parts, and aerospace components.
This process is particularly well-suited for thermoset materials, such as phenolics and melamine, which harden and become rigid when heated and pressed. The process is also used for some thermoplastics, such as polyethylene and polypropylene, which can be moulded using a variant of compression moulding called injection-compression moulding. Compression moulding is popular due to its low cost and high production volumes. The tooling is also generally cheaper than in injection moulding due mainly to the less sophisticated designs.
Pros and cons of Compression Moulding
Compression moulding is a versatile manufacturing process that offers both advantages and disadvantages. On the one hand, it is a cost-effective method for producing high-quality, consistent parts with excellent dimensional stability. As mentioned above, the tooling costs are generally lower than when using injection moulding, however, the cycle time is usually a lot longer too, depending on how thick the material is.
Although there is a wide selection of materials that can be used, the choice is more limited than when compared to injection moulding. The most common materials used are silicone, high-density polyethylene (HDPE) and polyurethane (PU).
Examples of common products
- Bakelite products: Bakelite is a type of thermosetting plastic that was commonly used in early electrical devices, such as switches and knobs. Bakelite products can be made using compression moulding.
- Brake pads: Some types of brake pads for automobiles and other vehicles are made using compression moulding. This process allows to produce durable, heat-resistant parts.
- Hockey pucks: Hockey pucks are typically made using vulcanized rubber that is moulded using compression moulding. This process allows for the creation of uniform, durable pucks that can withstand the impact of high-speed play.
- Composite materials: Compression moulding is also used to create composite materials, which are made by combining two or more materials with different properties to create a new material with improved characteristics. Composite materials can be used in a wide range of applications, including aerospace, construction, and sports equipment.
3. Plastic Moulding Methods: Blow Moulding
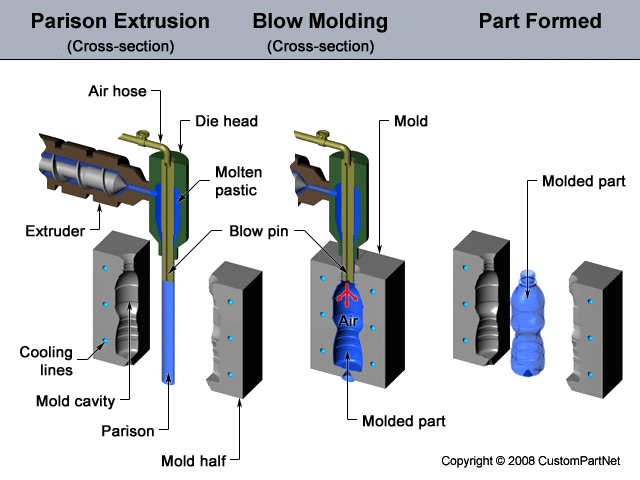
Blow moulding is a plastic moulding process used to create hollow objects, such as bottles or containers. The process begins with melting plastic pellets and extruding them into a tube-like shape called a parison. The parison is then clamped into a mould, and compressed air is blown into it to expand the plastic and conform it to the shape of the mould. Once the plastic has cooled and solidified, the mould is opened and the finished product is removed.
Blow moulding was first developed in the 1930s and has since become a popular manufacturing technique due to its ability to produce complex shapes quickly and efficiently. The process can accommodate a range of materials, including polyethylene terephthalate (PET), high-density polyethylene (HDPE), and polypropylene (PP), among others.
Blow moulding sets itself apart from other plastic moulding techniques because it is ideal for making smaller hollow parts with consistent wall thicknesses, such as containers, plastic bottles and other consumer goods.
As we shall see in the next paragraph, rotational moulding is also used to mould hollow products, but usually much larger products than what blow moulding can make.
Pros and Cons of Blow Moulding
There are both positive and negative aspects to the manufacturing process known as blow moulding. One of its benefits is its ability to facilitate high production efficiency, allowing for mass production of identical parts. It can also be utilized with a variety of materials, making it a flexible option for designing and enhancing functionality. In addition, blow moulded parts tend to be lightweight, making them well-suited for applications where weight is a concern, such as packaging and automotive components. Cost-effectiveness is another advantage of the process for large production runs, with lower costs per unit for larger quantities, and automation can increase productivity.
On the other hand, blow moulding does have some drawbacks. The process does not allow for particularly complicated designs, and the wall thicknesses need to be fairly consistent. However, one of the most important aspects to consider is the plastic waste generated by blow moulding, which can have harmful environmental impacts if not properly disposed of or recycled. Plastic bottles are among the worst products in terms of environmental impact, this however, should be considered more of a social/education problem than an issue with the process itself.
Examples of common products
- Plastic Bottles: plastic bottles are a common sight in our everyday lives. They are used for various products such as water, soda, shampoo, and more. Blow moulding is the primary process used to produce plastic bottles. It involves melting plastic pellets and extruding them into a tube-shaped parison. The parison is then placed in a mould, and air is blown into it to create the desired shape.
- Plastic Containers: plastic containers are used for storing and transporting various products, such as food, cleaning supplies, and automotive fluids. The process for producing these containers is similar to that of plastic bottles.
- Plastic Toys: Blow moulding is also used to produce plastic toys. The process involves creating a mould in the desired shape of the toy, then extruding plastic into the mould. The plastic is then cooled and hardened to maintain its shape.
- Automotive Parts: Blow moulding is used to produce various automotive parts, including fuel tanks, air ducts, and dashboards. The process for producing these parts involves extruding plastic into a mould and blowing air into it to create the desired shape.
- Medical Devices: Blow moulding is also used to produce medical devices such as catheters, IV bags, and oxygen masks. The process for producing these products involves extruding plastic into a mould and blowing air into it to create the desired shape.
4. Plastic Moulding Methods: Rotational Moulding
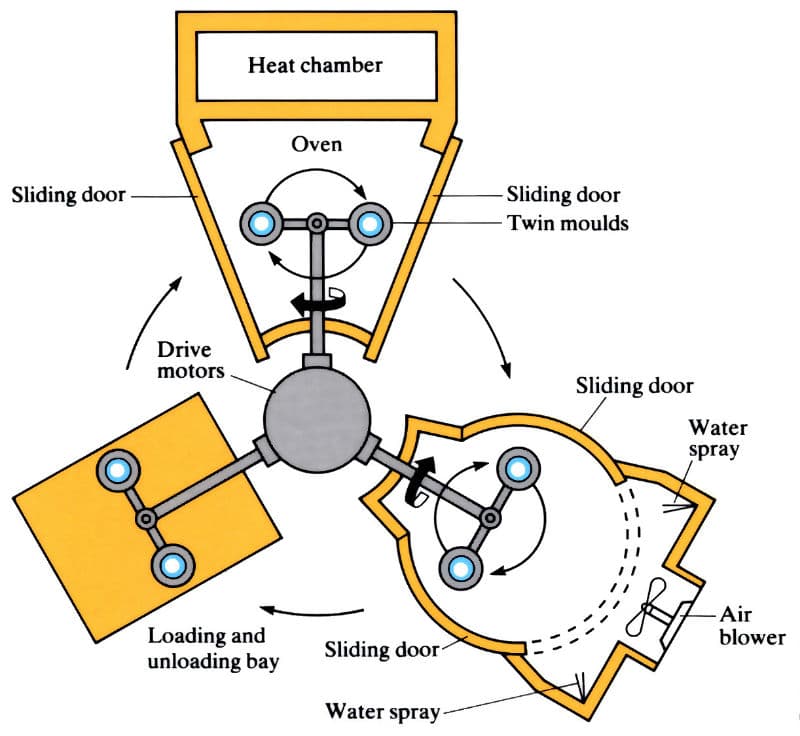
Rotational moulding, also known as roto moulding, is a plastic moulding process that involves heating a hollow mould, then rotating it on two perpendicular axes while the material is added and melted inside the mould. This process was first used in the 1850s to produce artillery shells and other hollow objects. In the early 1900s the development of this process led way to the production of hollow Easter eggs. It wasn’t until the 50s that plastic material was first used with the process and one of its first applications was moulding doll heads. With further developments in the technology more products could be manufactured, from traffic cones to automotive parts and fuel tanks.
Today, rotational moulding is still a very common process and it is used for producing a wide range of products, including large storage tanks, playground equipment, and consumer goods. Rotational moulding can be used with a variety of materials, including polycarbonate (PC), polyethylene (PE), polyvinyl chloride (PVC), and nylon (PA). The process can be used to produce large, complex parts with varying thicknesses and shapes, making it a popular choice for producing products that require high design flexibility.
Pros and Cons of Rotational Moulding
One of the biggest benefits of this process is its ability to achieve high design flexibility, enabling the creation of complex shapes and designs that may not be possible with other manufacturing processes. This is especially useful for creating products such as storage tanks, playground equipment, and furniture. Additionally, rotational moulding can create parts with consistent wall thickness and work with a wide range of materials, making it a flexible option for designing and enhancing functionality in various products. Rotational moulding is also a highly efficient process that allows for mass production of identical parts with minimal variation in quality. Like the other moulding processes, tooling is required for making moulds, and these can be expensive, especially for large parts. This generally leads also to longer moulding cycles.
Examples of common products
- Water Tanks: Rotational moulding is commonly used to produce water tanks for residential and commercial use.
- Playground Equipment: Rotational moulding is also used to produce playground equipment such as slides and tunnels.
- Kayaks and Canoes: Rotational moulding is used to produce kayaks and canoes because it can create a lightweight and durable product thanks to its wide selection of plastic materials.
- Traffic Cones: Rotational moulding is used to produce traffic cones.
- Insulated Coolers: Rotational moulding is also used to produce insulated coolers for camping and outdoor activities.
5. Plastic Moulding Methods: Thermoforming
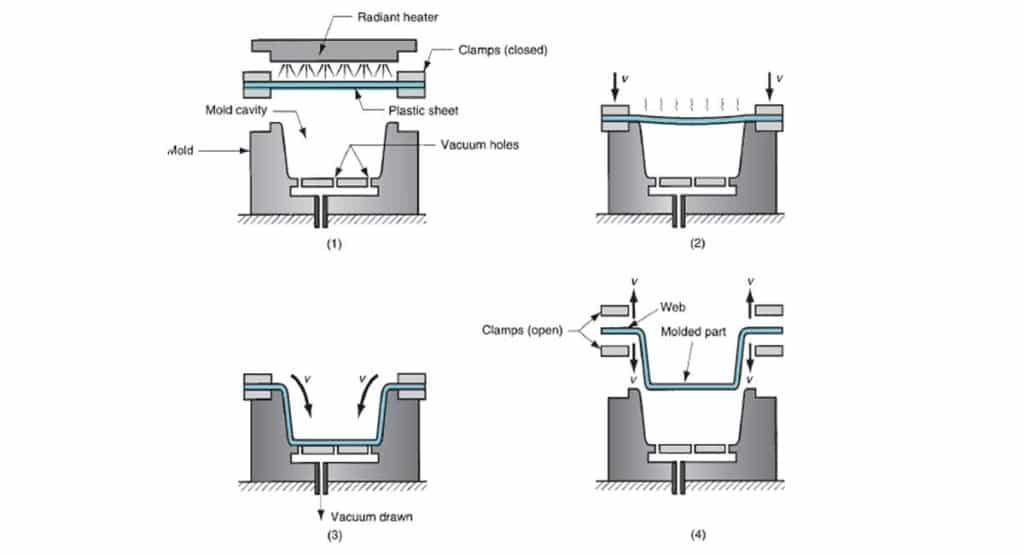
Thermoforming is a plastic moulding process that involves heating a plastic sheet to its softening point, then shaping it over a mould. The plastic is then cooled, and the final product is trimmed and removed from the mould. This method has been used for producing plastic parts since the 1940s and has since become a popular choice for producing a wide range of plastic products.
In the early days of thermoforming, only a limited range of materials were available, such as PVC, polystyrene, and polyethylene. However, advancements in material technology have since expanded the range of materials that can be used in thermoforming, including ABS, PET, and polycarbonate.
Thermoforming is commonly used for producing a wide range of products, including plastic trays, lids, clamshell packaging, and food packaging containers. The process is relatively fast and cost-effective, making it ideal for producing large quantities of parts.
Pros and Cons for Thermoforming
Thermoforming offers numerous benefits over other manufacturing processes. Its high design flexibility allows for the creation of complex shapes and designs that may not be achievable with other methods. It also works with a wide range of materials, has low initial tooling costs, and can produce parts quickly. Moreover, thermoformed products are highly recyclable, making them more environmentally friendly.
Despite its advantages, thermoforming has some limitations. It may have limited control over wall thickness, precision, and material selection, which may not be suitable for certain applications. Thermoformed parts may also be less durable and have lower impact resistance than those produced through other methods. Additionally, while thermoforming is recyclable, the use of plastic materials during production can still have a negative environmental impact.
Examples of common products
- Packaging Trays: Thermoforming is commonly used to produce packaging trays for food, medical supplies, and electronics. The process involves heating a sheet of plastic and forming it into a mould to create a tray that fits the specific product. The tray is then cooled and removed from the mould.
- Automotive Interior Parts: Thermoforming is often used to produce interior automotive parts, such as dashboards, door panels, and consoles.
- Medical Devices: Thermoforming is also used to produce certain medical devices, for example trays, containers, and surgical instruments.
- Signs and Displays: Thermoforming can be used to produce signs and displays for advertising and marketing purposes.
Conclusion
The choice of moulding method can significantly affect the outcome of the production process. For instance, in broader terms, injection moulding is suitable for producing complex shapes with high precision, while compression moulding is suitable for producing fairly large parts. Blow moulding is excellent for producing hollow parts and rotational moulding is perfect for producing large, hollow, and complex-shaped products. Thermoforming is an ideal method for producing large parts with low tooling costs. However, all these processes are very different from one another and the process to be used is mostly dictated by the design of the part needing to be moulded and the material it is to be made of.
Understanding these processes can allow engineers and designers to develop products that are optimised for the production process used to make them, thus saving lots of time and money in the development stages. Learn more about leveraging moulding in the right context by speaking to a professional today.