Have you ever wondered about the intricate process behind the creation of airplanes? How are these magnificent flying machines designed and manufactured to meet the highest standards of safety and performance? Aerospace fabrication lies at the heart of this remarkable endeavor, encompassing a multitude of disciplines and techniques to bring these engineering marvels to life. From the historical evolution of aerospace fabrication to the innovative use of advanced materials and manufacturing methods, understanding the intricacies of airplane production unveils a world of ingenuity, precision, and technological advancements. In this paper, we will explore the journey of how airplanes are made, shedding light on the conceptualization, design, materials, and manufacturing processes that contribute to their creation. By delving into the fascinating world of aerospace fabrication, we can gain a deeper appreciation for the remarkable feats of engineering that enable human flight.
Since the advent of powered flight in the early 20th century, aerospace fabrication has evolved significantly, driven by advancements in technology, engineering principles, and materials science. From the early days of wood and fabric construction to modern composite structures, the aerospace industry has continuously pushed the boundaries of innovation to enhance aircraft performance, fuel efficiency, and passenger safety.
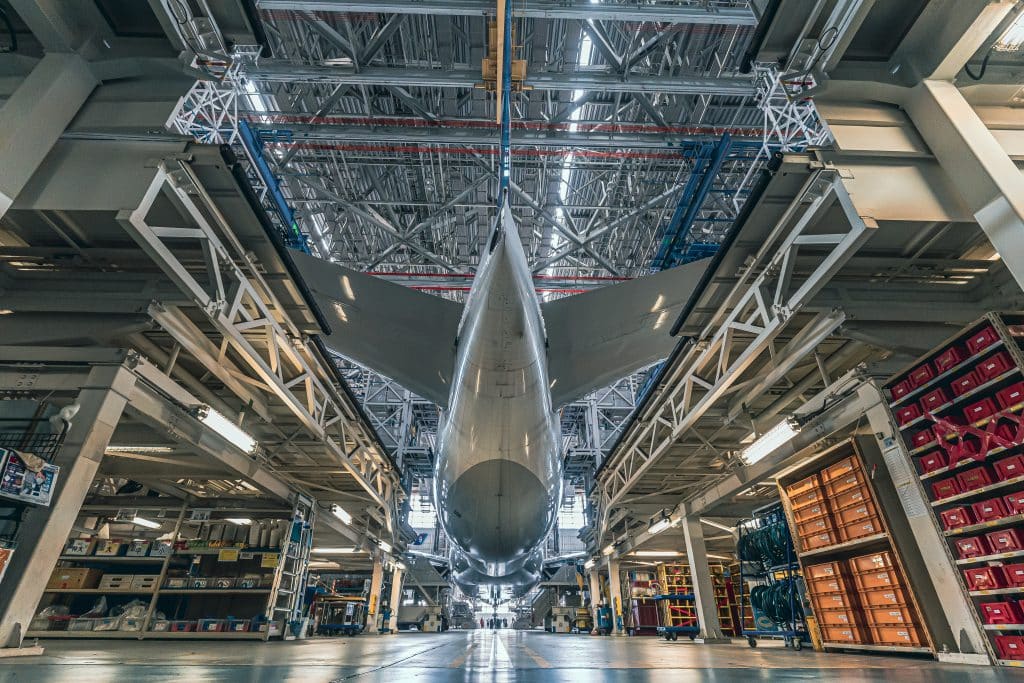
History of Aerospace Fabrication
Wright Brothers: Pioneers of Aviation
The history of aerospace fabrication traces back to the pioneering efforts of Orville and Wilbur Wright, who are credited with achieving the first controlled, powered flight in 1903. The Wright brothers’ groundbreaking accomplishment at Kitty Hawk, North Carolina marked a monumental turning point in human history, sparking a rapid progression in aviation technology and the development of aerospace fabrication techniques.
Prior to the Wright brothers’ achievement, aviation was a realm of experimentation and imagination. However, it was their meticulous engineering approach and innovative design principles that set them apart. The Wright brothers recognized the importance of not only developing a powered aircraft but also understanding the principles of flight, control, and stability. They extensively researched the behavior of wings, propellers, and airfoil shapes, conducting wind tunnel experiments and building their own wind tunnel to test their theories.
Their relentless dedication to refining their designs led to the creation of the Wright Flyer, a biplane with a wooden framework and fabric covering. This aircraft featured a sophisticated control system, including wing-warping and a movable rudder, which allowed the pilot to maintain stability and control during flight. The Wright brothers’ emphasis on precision engineering and attention to detail laid the foundation for subsequent advancements in aerospace fabrication.
Conceptualization and Design of Airplane
In today’s timeline, airplanes have come a long way, evolving from the humble beginnings of aviation to highly sophisticated flying machines. The conceptualization and design phase plays a pivotal role in shaping the performance, efficiency, and safety of modern aircraft. Engineers and designers employ a comprehensive approach, considering factors such as aerodynamics, weight distribution, and safety throughout the design process.
Aerodynamics
One of the key considerations in the conceptualization and design of an airplane is aerodynamics—the study of how air flows around the aircraft and the forces acting upon it. Engineers use computer simulation and wind tunnels to test and refine the design ensuring that the airplane will fly efficiently and safely. Engineers and designers strive to optimize the aerodynamic performance of an airplane to minimize drag, enhance lift, and improve fuel efficiency. This involves shaping the aircraft’s surfaces, such as wings, fuselage, and control surfaces, to ensure smooth airflow and reduce resistance.
For example, the design of the Boeing 787 Dreamliner incorporates several aerodynamic features to maximize performance. Its wings are swept back, reducing drag and improving lift-to-drag ratio. The wingtips are also equipped with winglets, which help minimize the formation of vortices and further reduce drag.
Weight Distribution
Effective weight distribution is another critical aspect of airplane design. Engineers carefully distribute the weight of the aircraft to maintain stability, maneuverability, and structural integrity. The position of major components, such as engines, fuel tanks, and cargo, must be strategically determined to ensure the airplane maintains its balance throughout various flight conditions.
As an illustration, the Airbus A380, the world’s largest passenger aircraft it has double deck layout allowing for more seating and reducing noise level coming from the passengers. Its engines are located on the wings to distribute their weight evenly and maintain lateral stability. Additionally, the fuel tanks are positioned in a way that optimizes balance during flight, accounting for the consumption of fuel as the aircraft travels.
Safety
Ensuring the safety of an airplane is of paramount importance during the conceptualization and design phase. Aircraft manufacturers adhere to stringent safety regulations and employ a variety of design features to protect passengers and crew. These features include fire-resistant materials, redundant systems, emergency exits, and advanced avionics for navigation and communication.
For instance, the Boeing 777X incorporates advanced safety measures, such as an improved fire detection and suppression system, redundant flight control surfaces, and enhanced emergency evacuation capabilities. These design considerations help mitigate risks and ensure the safety of passengers and crew in the event of an emergency.
Structural Design and Materials Used in Aerospace Fabrication
Structural Design Phase
Once the initial design is approved, engineers move on to the structural design phase. They determine the optimal materials and construction methods for different sections of the aircraft, such as the fuselage, wings, tail, and landing gear. Modern airplanes predominantly use lightweight yet strong materials like aluminum alloys, composite materials (carbon fiber-reinforced polymers), and titanium.
The structural design considers the forces and stresses that an aircraft will experience during flight, including lift, drag, weight, and thrust. Engineers employ advanced mathematical models and computer simulations to ensure the structural integrity of the aircraft. Finite element analysis (FEA) is often used to simulate stress distribution and identify potential weak points in the structure.
For example, the Airbus A350 XWB incorporates advanced structural design and materials. Its fuselage is primarily constructed using carbon fiber-reinforced polymer composites, which offer high strength-to-weight ratio and corrosion resistance. This allows for lighter and more fuel-efficient aircraft. The wings of the A350 XWB feature a composite structure, reducing weight and enhancing aerodynamic efficiency.
Materials Used in Aerospace Fabrication
A crucial aspect of aerospace fabrication is the selection and utilization of suitable materials that can withstand the demanding conditions encountered during flight. The materials used in aircraft and spacecraft construction vary depending on their specific properties and performance requirements. Here are the Metallic and Non-Metallic materials that are commonly used for Aerospace fabrication.
Metallic Materials
Alloys
Alloys play a vital role in the aircraft industry, as they offer a range of properties that pure metals alone cannot provide. An alloy is formed by combining two or more metals, with the base metal being the primary constituent. The other metals added to the base metal are known as alloying elements. The addition of alloying elements can significantly alter the properties of the base metal. For instance, pure aluminum is relatively soft and weak, but the addition of small amounts of copper, manganese, and magnesium greatly enhances its strength. Heat treatment further modifies the strength and hardness of alloys.
Aluminum
Aluminum alloys are extensively utilized in modern aircraft construction due to their high strength-to-weight ratio. These alloys are corrosion-resistant and relatively easy to fabricate. The outstanding characteristic of aluminum is its lightweight nature, contributing to improved fuel efficiency and overall performance of aircraft. Its application ranges from structural components to fuselage and wing structures.
Magnesium
As the lightest structural metal in the world, magnesium offers exceptional weight-saving advantages. Weighing two-thirds as much as aluminum, magnesium is utilized in the construction of helicopters. However, its susceptibility to corrosion has limited its use in conventional aircraft applications.
Titanium
Titanium is a lightweight and strong metal with excellent corrosion resistance. Recent developments have made titanium an ideal choice for applications where aluminum alloys are insufficiently strong or stainless steel is excessively heavy. Titanium exhibits remarkable durability even after prolonged exposure to seawater and marine environments, making it highly suitable for critical aerospace components.
Steel Alloys
Steel alloys employed in aircraft construction possess exceptional strength to withstand the forces encountered during flight. These alloys contain small percentages of carbon, nickel, chromium, vanadium, and molybdenum. High-tensile steels can withstand stresses ranging from 50 to 150 tons per square inch without failure. Such steels are commonly formed into tubes, rods, and wires. Stainless steel, another widely used type, offers corrosion resistance, making it particularly valuable for aerospace applications in or near water.
Nonmetallic materials
Transparent Plastic
Transparent plastic is utilized in the fabrication of canopies, windshields, and other transparent enclosures in aircraft. Care must be taken when handling transparent plastic surfaces as they are relatively soft and prone to scratching. At around 225°F, transparent plastic becomes soft and pliable, necessitating temperature considerations during manufacturing and maintenance processes.
Reinforced Plastic
Reinforced plastic finds application in the construction of radomes, wingtips, stabilizer tips, antenna covers, and flight controls. It offers a high strength-to-weight ratio and is resistant to mildew and rot. Reinforced plastic is a sandwich-type material consisting of two outer facings made up of multiple layers of glass cloth bonded together with a liquid resin. The center layer comprises a honeycomb structure made of glass cloth. Due to its ease of fabrication, reinforced plastic is suitable for various other parts of the aircraft as well.
Composite and Carbon Fiber Materials
For high-performance aircraft that require an exceptional strength-to-weight ratio, composite materials are fabricated to meet these specific demands. Composite materials are constructed using layers of bonding materials, such as graphite epoxy or boron epoxy, mechanically fastened to conventional substructures. Another type of composite construction involves thin graphite epoxy skins bonded to an aluminum honeycomb core. Carbon fiber, an extremely strong and thin fiber, is produced by heating synthetic fibers like rayon until charred and then layering them in cross-sections.

Manufacturing Components for Airplanes
Fuselage: Automated Robotics
The manufacturing process of airplane components involves a combination of advanced technologies and skilled craftsmanship. Automated robotics play a crucial role in fabricating the fuselage, the main body structure of an aircraft. These robots precisely cut, shape, and join metal or composite panels, ensuring high precision and efficiency in production. The use of robotics allows for increased consistency and accuracy in the manufacturing process, resulting in improved quality and reduced production time.
For instance, in the production of the Boeing 777X, automated robotic systems are employed to assemble the fuselage sections. These robots precisely position and rivet the large panels together, ensuring a seamless and structurally sound fuselage.
Wings: Aluminium Extrusion and Carbon Fiber Composites
The wings of an airplane undergo specialized manufacturing processes to achieve optimal strength, aerodynamic efficiency, and weight reduction. Aluminum extrusion is a common technique used for fabricating wing components. Extrusion involves shaping aluminum alloy through a die to form complex profiles and structural shapes. This method provides lightweight yet robust wing structures.
Moreover, the increasing utilization of carbon fiber composites in wing manufacturing has revolutionized the aerospace industry. Carbon fiber composites offer exceptional strength-to-weight ratio, allowing for lighter wings that enhance fuel efficiency. Manufacturers employ advanced techniques like automated tape laying and resin infusion to create precise carbon fiber composite wing structures.
Engines
The manufacturing of airplane engines encompasses a wide range of metalworking and machining operations, each playing a crucial role in producing reliable and high-performance powerplants. Virtually every common metalworking and machining operation is used in aircraft engine manufacture. This includes hot forging for shaping critical components such as airfoils and compressor disks. Casting is employed for the production of structural components and engine frames, ensuring the integrity and strength of these vital parts.
Furthermore, a variety of machining processes such as grinding, broaching, turning, drilling, milling, shearing, sawing, threading, welding, and brazing are employed throughout the engine manufacturing process. These operations contribute to the precise fabrication of engine components, allowing for optimal performance and durability.
For example, in the manufacturing of turbine blades, high-precision machining techniques are utilized to create intricate airfoil shapes, which are crucial for efficient energy extraction from the high-velocity exhaust gases.
Landing Gear
The manufacturing of landing gear involves the production of sturdy and reliable components capable of withstanding the forces and stresses experienced during takeoff, landing, and ground operations. High-strength materials like steel and titanium are commonly used in the construction of landing gear components, ensuring durability and structural integrity.
Conclusion
Aerospace fabrication is a remarkable process that encompasses the conceptualization, design, and manufacturing of airplanes. From the pioneering efforts of the Wright brothers to the cutting-edge technologies used today, this field has continuously pushed the boundaries of innovation in pursuit of safe, efficient, and high-performance aircraft. Engineers and designers meticulously consider factors such as aerodynamics, weight distribution, and safety to create airplanes that can soar through the skies with stability and grace. The choice of materials, including lightweight aluminum alloys, composite materials like carbon fiber-reinforced polymers, and titanium, contributes to the strength and efficiency of the aircraft’s structure. Through specialized manufacturing techniques, such as automated robotics for fuselage fabrication and advanced machining and casting processes for engine components, the industry ensures precision, durability, and reliability in the manufacturing of airplane parts. Aerospace fabrication stands as a testament to human ingenuity, engineering prowess, and unwavering commitment to excellence, allowing us to witness the marvels of flight and experience the wonders of modern aviation.