Many businesses rely on Asian manufacturing supply chain to produce and deliver their goods and services. A supply chain is a network of activities, people, and resources that starts with raw materials and ends with finished products in the hands of customers. A good supply chain can help a business compete globally and meet customer needs by lowering costs, improving quality, increasing efficiency, and creating value.
One of the most important regions for supply chains is Asia. Asia is the world’s manufacturing hub, producing and exporting a wide range of goods and services. In 2019, Asia was responsible for 60% of the world’s manufacturing output and 40% of the world’s manufacturing value added. Asian manufacturers have expertise in various sectors, such as electronics, textiles, automobiles, machinery, chemicals, and more. They also contribute to innovation, productivity, and economic growth in the region and beyond.
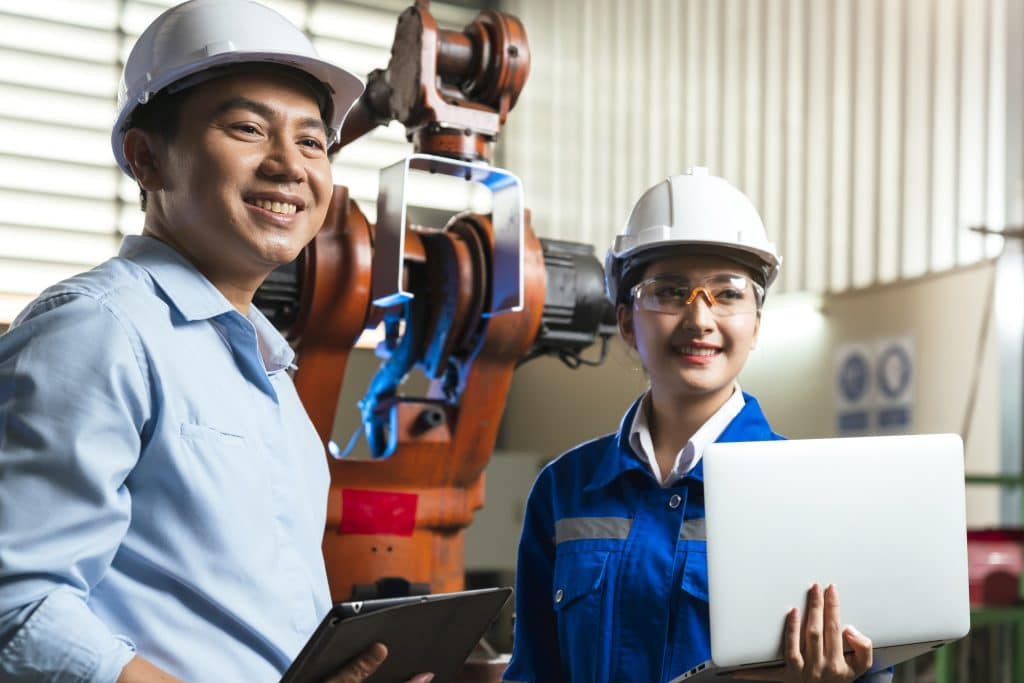
Historical Evolution of Asian Manufacturing Supply Chain
Early Developments and Contributions
Asian manufacturing has a long and rich history that dates back to ancient times. Some of the earliest examples of Asian manufacturing include silk production in China, cotton weaving in India, pottery making in Japan, and metalworking in Korea. These products were traded across Asia and beyond, creating cultural and economic exchanges. Asian manufacturing also contributed to the development of science, technology, art, and culture in the region and the world.
The Rise of Asian Manufacturing Hubs
In the second half of the 20th century, Asian manufacturing underwent a rapid transformation and expansion. Several factors contributed to this process, such as industrialization policies, foreign investment, trade liberalization, regional integration, labor migration, and technological advancement. As a result, some Asian countries emerged as global manufacturing hubs that specialized in different sectors and stages of production. For example, Japan became a leader in high-tech industries, such as electronics and automobiles; Taiwan and South Korea became known for their semiconductor and display industries; Hong Kong and Singapore became centers for trade and finance; China became the world’s factory for mass production; and Southeast Asian countries became sources of low-cost labor and raw materials.
Key Countries and Regions in Asian Manufacturing Supply Chain
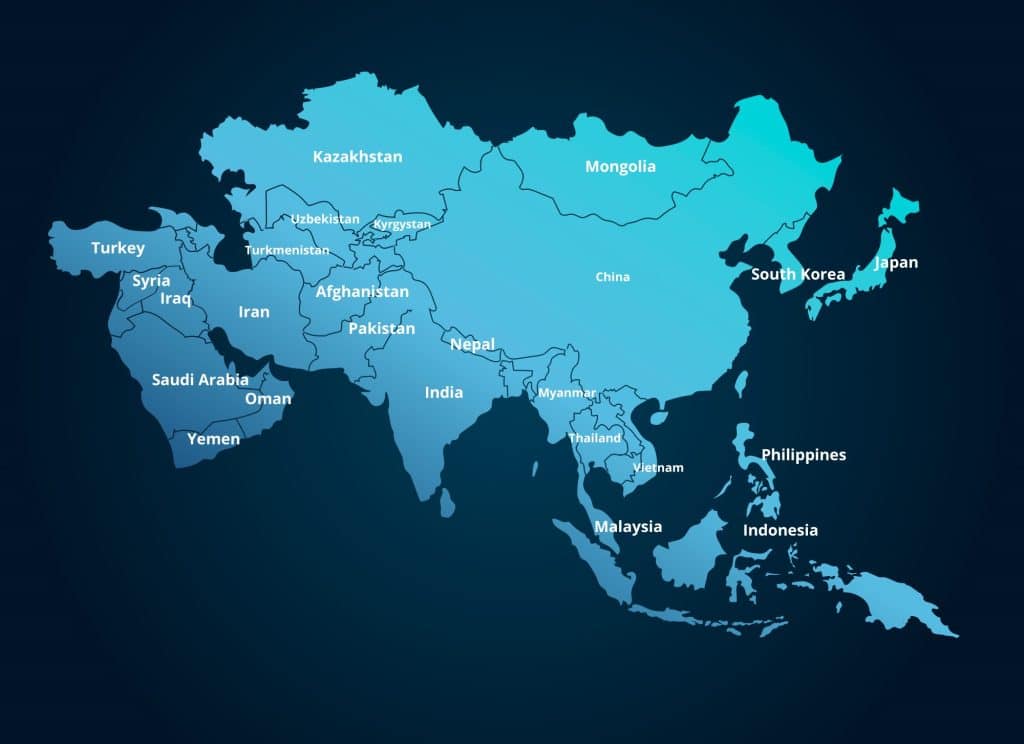
China: The Manufacturing Giant
China is the largest manufacturer in the world by output value, accounting for 28% of the global total in 2019, according to Statista. China’s manufacturing sector is diverse and covers a wide range of industries, such as machinery, electrical equipment, textiles, chemicals, metals, vehicles, and more. China’s manufacturing success is attributed to its large domestic market, abundant labor force, low production costs, extensive infrastructure, supportive government policies, and strong export orientation.
According to the International Organization of Motor Vehicle Manufacturers (OICA), China produced 25.7 million passenger cars and 4.4 million commercial vehicles in 2019, making it the world’s largest automobile producer. China’s electronics industry is also the largest in the world, producing more than 40% of global consumer electronics output in 2019. China is also a major producer of machinery and equipment, such as industrial robots, machine tools, power generators, and construction machinery.
In 2019, China’s machinery industry output value reached 30.5 trillion yuan (about 4.4 trillion US dollars), accounting for 29.6% of the country’s total industrial output value. China’s medical device industry is one of the fastest-growing sectors in the country, with an annual growth rate of over 20% in recent years. In 2019, China’s medical device market size reached 671.3 billion yuan (about 97 billion US dollars), ranking second in the world after the United States. China’s metal fabrication industry is also an important part of its manufacturing sector, producing various metal products such as pipes, wires, cables, fasteners, springs, and castings. In 2019, China’s metal fabrication industry output value reached 7.8 trillion yuan (about 1.1 trillion US dollars), accounting for 7.6% of the country’s total industrial output value.
China’s manufacturing industry is a key driver of its economic growth and development, as well as a major source of employment and income for its people. China’s manufacturing industry also faces some challenges and opportunities in the future, such as upgrading its technology and innovation capabilities, improving its environmental performance and sustainability, and adapting to changing domestic and international market demands.
Southeast Asian Countries: Emerging Hubs
Southeast Asian countries are also important players in the Asian manufacturing supply chain. According to S&P Global, Southeast Asia’s share of global manufacturing output increased from 3% in 2000 to 6% in 2018. Some of the leading countries in this region include Vietnam, Thailand, Indonesia, Malaysia, and the Philippines.
These countries have attracted foreign investment and trade by offering competitive advantages such as low labor costs, strategic geographic location, favorable business environment, and growing consumer demand. Some of the key sectors that these countries specialize in include electronics, textiles, footwear, furniture, and automotive.
One of the notable examples of a successful manufacturing hub in Southeast Asia is Vietnam. Vietnam has emerged as a major exporter of electronics, machinery, and medical devices, thanks to its skilled workforce, stable political system, and preferential trade agreements.
According to BCG, Vietnam’s exports of machinery and electronics grew by 23% annually from 2015 to 2019, making it the second-largest exporter in ASEAN after Singapore. Vietnam also ranked fourth in ASEAN in terms of medical device exports, with a growth rate of 26% annually in the same period. Vietnam’s automotive industry is also developing rapidly, with a domestic production capacity of over 200,000 vehicles per year and a local content ratio of over 40%.
Southeast Asia’s manufacturing potential is further enhanced by the Regional Comprehensive Economic Partnership (RCEP), which is expected to lower tariffs, harmonize standards, and facilitate cross-border investment among 15 countries in Asia-Pacific. RCEP will create a market of 2.2 billion people and a combined GDP of $26.2 trillion, accounting for nearly 30% of the world’s population and economy. RCEP will also help ASEAN manufacturers diversify their supply chains and access new markets, especially in China, Japan, South Korea, and Australia.
Southeast Asia has a strong manufacturing foundation and a bright future ahead. By embracing Industry 4.0 technologies and green practices, ASEAN manufacturers can move up the value chain and become global leaders in their fields.
Many big US based corporations are manufactured in Asia, for example Apple, Boeing and Honeywell all have their products made in Asia. Over the past few years, with the Covid pandemic and the rising tensions between the US and China, several large companies are slowly onshoring or moving to other South East Asian countries like Vietnam, Thailand and Indonesia. Despite this, China still remains the most popular choice for manufacturers looking to scale up and achieve cost reductions through offshore manufacturing.

Strategies for Optimizing Engagement with Asian Manufacturers
Building Strong Supplier Relationships
One of the main challenges that businesses face when engaging with Asian manufacturers is managing the quality, reliability, and communication of their suppliers. To overcome this challenge, businesses need to build strong supplier relationships that are based on trust, transparency, and mutual benefit. Some of the ways to achieve this include:
- Conducting due diligence and background checks on potential suppliers.
- Visiting supplier facilities and verifying their capabilities and certifications.
Collaborating with Offshore Manufacturing Companies
Another way to optimize engagement with Asian manufacturers is to collaborate with an offshore manufacturing company that can act as a bridge between the business and its suppliers.
An offshore manufacturing company is a third-party service provider that offers end-to-end solutions for sourcing, manufacturing, and delivering products from Asia to the business’s destination. Some of the benefits of working with an offshore manufacturing company include:
- Accessing a network of vetted and qualified suppliers that match the business’s needs.
- Leveraging the expertise, experience, and local knowledge of the offshore manufacturing company Reducing risks, costs, and lead times by outsourcing non-core activities.
- Enhancing flexibility, scalability, and responsiveness by adjusting production volumes and specifications according to demand.
- Improving customer satisfaction by ensuring consistent quality and timely delivery.
Managing Quality Control from Afar
Quality control is a critical aspect of engaging with Asian manufacturers, especially when the business is located far away from its suppliers. Quality control refers to the process of ensuring that the products meet the specifications and standards of the business and its customers. To manage quality control from afar, businesses need to implement effective strategies such as:
- Providing drawings with all the requirements clearly specified on them. And also making sure these are understood by the factory representative and communicated to the shop floor.
- Conducting pre-production, in-process, and post-production inspections and audits.
- Using third-party inspection agencies or independent quality inspectors to verify the products.
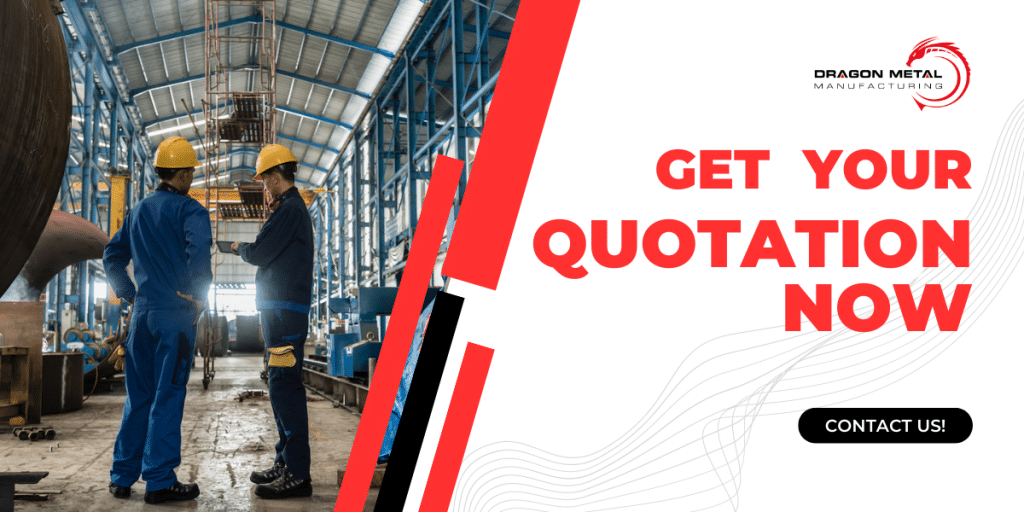
Embrace the Potential of the Asian Manufacturing Supply Chain
Asian manufacturing is a key driver of global business growth and innovation. Businesses that want to thrive in the international market need to understand the origins, features, and directions of Asian manufacturing. This will help them find the best opportunities and partners for their products and services. They also need to use effective strategies to work with Asian manufacturers and improve their supply chain performance. This will help them deliver value to their customers and stakeholders. If you are looking for a reliable and experienced offshore manufacturing partner in Australia, contact us today. We have the expertise, network, and resources to help you achieve your business goals with Asian manufacturing.