In today’s competitive market, efficient and cost-effective production is essential for manufacturers looking to stay ahead of the competition. Component manufacturing plays a crucial role in achieving these goals, as it involves the production of individual parts that are used to build larger sub-assemblies or finished products. Whether a manufacturer produces these components in-house or outsources them to third-party suppliers, the quality and efficiency of the component manufacturing can have a significant impact on the overall success of their business.
One of the key challenges of component manufacturing is balancing cost, quality, and efficiency. On the one hand, manufacturers need to keep costs low in order to remain competitive and profitable. On the other hand, they also need to ensure that the components they produce, or source, meet the necessary quality standards and specifications. At the same time, they must maintain a high level of efficiency to meet production schedules and deliver products on time.
To overcome these challenges, manufacturers have several choices when it comes to component manufacturing. Some may choose to make everything in-house, while others may outsource certain components or entire sub-assemblies. The decision of whether to insource or outsource component manufacturing depends on a range of factors, including the manufacturer’s capabilities, the complexity of the components, and the cost and availability of suppliers.
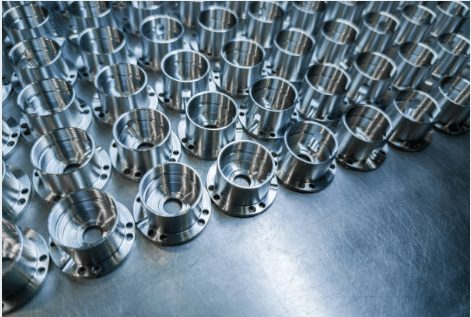
Outsourcing Component Manufacturing
The Benefits of Working with a Specialized Component Manufacturer
Working with a specialized component manufacturer can provide several advantages for manufacturers. Specialized manufacturers have the expertise and equipment required to produce high-quality components efficiently, reliably, and cost-effectively. For example, a company that specializes in packaging will be better equipped to make for example a new plastic container packaging than a general manufacturing facility. By outsourcing to a specialized component manufacturer, manufacturers can take advantage of economies of scale and benefit from the expertise and innovation that specialized manufacturers bring to the table.
When is it More Cost-Effective to Outsource Component Manufacturing?
Outsourcing component manufacturing becomes a cost-effective option under specific circumstances. Manufacturers may choose to outsource when they lack specialized expertise or the necessary equipment to produce certain components in-house. By partnering with specialized suppliers, manufacturers can leverage their capabilities and focus on their core competencies. Outsourcing is also beneficial when demand fluctuates, as external suppliers can more efficiently adjust production capacity. Furthermore, outsourcing can lead to cost savings through economies of scale, especially when working with suppliers that possess well-established supply chains and competitive pricing structures.
Why Outsourcing is a Viable Option for Component Manufacturing
In-house manufacturing grants manufacturers direct control over the entire production process, enabling them to ensure quality, customization, and safeguard intellectual property. It also provides the flexibility to adapt to changing demands and refine product designs. However, establishing and maintaining an in-house manufacturing operation requires substantial investments in infrastructure, equipment, skilled labour, and ongoing operational expenses. This can pose challenges, particularly for smaller manufacturers or those specializing in niche markets.
Outsourcing component manufacturing is a viable option for manufacturers looking to reduce the amount of in-house labour, lower costs, or increase production capacity. It can also provide access to specialized expertise that the manufacturer may not have. Given the current challenges of finding skilled labour, outsourcing can be a strategic move for manufacturers. Fortunately, there are different options available for outsourcing. Manufacturers can choose to outsource locally and keep production in Australia, or they can opt for offshore outsourcing by working directly with factories overseas or with a local offshore manufacturing specialist. All three options can be great solutions depending on the manufacturer’s specific needs and situation.
Outsourcing Component Manufacturing to local suppliers
Outsourcing component manufacturing to local suppliers can provide several benefits for manufacturers. One of the key advantages is that local suppliers can offer a fast turnaround time, reducing lead times and allowing manufacturers to respond quickly to changing market demands. Additionally, working with local suppliers makes it easier to visit the supplier and discuss requirements face-to-face, which can improve communication and ensure that the components meet the manufacturer’s specifications. Communication can also be easier, as there may be fewer language barriers or time zone differences to contend with. This solution is usually ideal during the initial product development stages where the convenience outweighs the heftier price tag.
Outsourcing Component Manufacturing to offshore factories
Outsourcing component manufacturing to offshore factories can be a cost-effective option for manufacturers looking to reduce production costs. Many large manufacturers have set up factories overseas, where labour costs are lower and regulations may be less stringent. Going directly to overseas manufacturers can be the cheapest solution, but even smaller manufacturers can take advantage of this option by conducting thorough research and finding suitable suppliers. However, it is usually recommended to have a contact or partner in the country where the supplier is located to help navigate any language barriers or cultural differences.
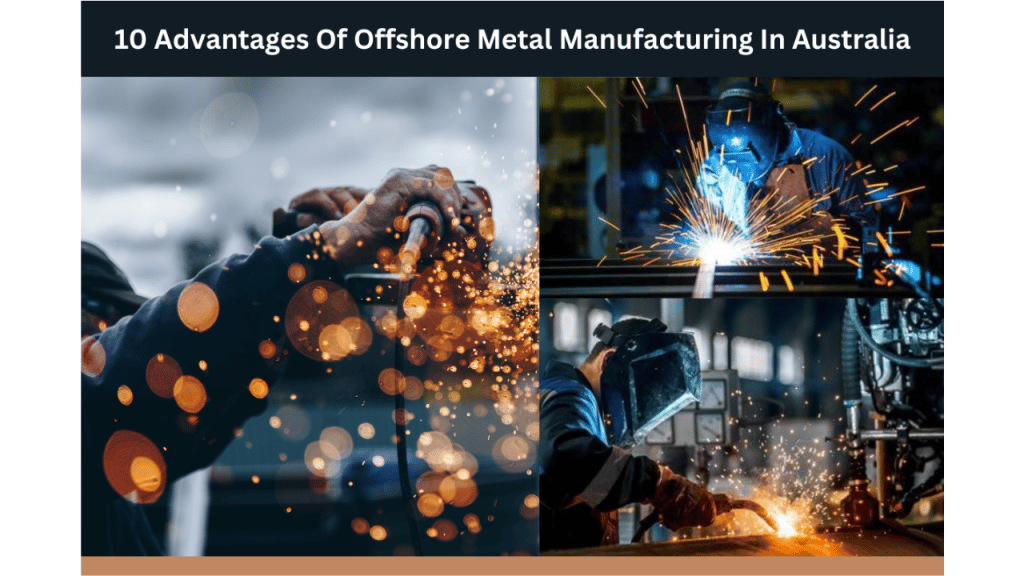
Outsourcing Component Manufacturing through local offshore manufacturing specialists
Outsourcing component manufacturing through local offshore manufacturing specialists can be a great option for Australian manufacturers who want to tap into the benefits of offshore manufacturing without taking on the associated risks. These specialists act as intermediaries between the manufacturer and the offshore factory, handling the project management, quality assurance, and some even help with logistics. Additionally, because these specialists handle a large volume of projects, they can often secure discounted prices from offshore suppliers, making them sometimes cheaper than going direct without the added risk.
What are the risks involved with Outsourcing Component Manufacturing
Outsourcing component manufacturing can be a great solution for manufacturers, but it does come with some risks.
- When outsourcing locally, the main challenge is price, as specialized Australian suppliers tend to be more expensive than offshore suppliers. Additionally, manufacturers may need to outsource several production processes, increasing the overall cost of the individual products further.
- When outsourcing to offshore factories, the main risks are communication breakdown and the possibility of receiving substandard quality. When things do go wrong, there may not be much that can be done to rectify issues without some kind of local presence.
- When using local offshore manufacturing specialists, the main disadvantage is that they are typically not set up for low-value and quick turnaround projects, such as prototyping and product development, and are more suitable for production and shipping by sea. Additionally, unlike some local suppliers who may offer special credit terms, these companies usually require a small upfront deposit.
Choosing the Right Components to Outsource
Identifying the right components to outsource is critical for manufacturers looking to optimize their supply chain and reduce costs. Manufacturers should focus on outsourcing components that are not critical to their core competencies or those that require specialized expertise or equipment. For example, a manufacturer of electronic products may choose to outsource the production of printed circuit boards, as this requires specialized equipment and expertise. Conversely, they may choose the outer enclosures and hardware components that are more closely aligned with their core competencies, and the final assembly of the product.
Understanding the Advantages and Disadvantages of Outsourcing Sub-Assemblies vs. Individual Components
Manufacturers can decide to outsource individual components or even sub-assemblies or even complete assemblies. Sub-assemblies refer to pre-assembled components that are used in the final assembly of a product, while individual components refer to discrete parts used in the production of sub-assemblies. Outsourcing sub-assemblies can provide greater efficiency in the overall production process, as it cuts down on a significant amount of time the manufacturer would otherwise need to produce all the individual components, test them, and assemble them. All these steps would be done by the supplier and the end manufacturer would just need to assemble it. On the other hand, if the assembly of certain components is critical and requires very accurate testing, it may be preferable to outsource the individual components and perform the testing and assembly in-house to have greater control over the process.

Tips for Optimizing Efficiency and Quality with Local or Offshore Suppliers
When working with local suppliers, it’s important to build a good relationship with them. Visit their facilities and ask for references from their clients. Discuss trading and payment terms, and agree on a clear plan for quality assurance, including who will be responsible for rectifying any issues that arise. When working with offshore suppliers, it’s crucial to do your due diligence and thoroughly research potential suppliers before committing. It’s also recommended to have a local agent or partner in the country to act as your representative, handle communication, and oversee production. In addition, use clear and concise communication methods to ensure that everyone is on the same page, and have a contingency plan in place in case of unforeseen delays or issues. By taking these steps, you can optimize efficiency and ensure quality with both local and offshore suppliers.
Sourcing Commercial Off-The-Shelf (COTS) Components
Sourcing Commercial Off-The-Shelf (COTS) components is another aspect of the manufacturing process that can be outsourced locally or offshore. Just like with custom manufacturing, sourcing locally can come with a higher price tag, but often guarantees that the product is certified and comes with a warranty. Directly sourcing products from overseas is also an option, either by contacting suppliers directly or by using a sourcing agent. Some offshore manufacturing companies even offer sourcing as a service. It is worth noting that for many products, equivalent off-the-shelf components and products can be found at a fraction of the cost of their Australian counterparts. With careful research and due diligence, manufacturers can find reliable suppliers of COTS components that offer both cost savings and quality assurance.
The Benefits of Sourcing COTS Components for Manufacturing
The adoption of COTS components offers several benefits to manufacturers. Firstly, it allows them to tap into existing designs and technologies, saving valuable time and resources that would otherwise be spent on developing custom components from scratch. By incorporating COTS components, manufacturers can accelerate their production cycles and meet tight deadlines. Moreover, cost savings can be realized through the utilization of mass-produced COTS components, benefiting from economies of scale. For instance, a consumer electronics manufacturer may choose to integrate COTS display panels instead of investing in the development of bespoke screens, resulting in lower costs and faster time-to-market.
Conclusion
Efficient and cost-effective component manufacturing plays a crucial role in the success of modern manufacturers. By carefully considering the options available and making informed decisions, manufacturers can optimize their production processes and stay competitive in the market. Here are the key takeaways for this blog:
- Evaluating the feasibility of outsourcing component manufacturing can lead to cost savings, access to specialized expertise, and increased scalability.
- Careful selection of the right components for outsourcing is essential, considering factors such as complexity, expertise required, and quality standards.
- When working with offshore component manufacturers, effective communication and quality control processes are vital to ensure successful outcomes.
- Sourcing commercial off-the-shelf components offers benefits such as reduced development time and access to standardized, reliable products.
- Finding the right balance between in-house and outsourced manufacturing is key to leveraging core competencies while maximizing efficiency and cost-effectiveness.
Component manufacturing forms the backbone of various industries, from automotive and electronics to medical devices and consumer goods. The ability to produce high-quality components efficiently is instrumental in meeting customer demands, driving innovation, and maintaining a competitive edge. Manufacturers must continuously evaluate their manufacturing strategies, adapt to market changes, and explore opportunities to optimize their component manufacturing processes.