Compression molding is a pivotal manufacturing technique utilized for crafting diverse plastic or composite parts. The process entails introducing a pre-measured and preheated material, such as a thermosetting polymer or thermoplastic compound, into an open mold cavity. Subsequently, the mold is sealed, and significant pressure is exerted to compress the material into the desired shape, often accompanied by heat to aid in curing or melting.
In this blog post, we will delve into several key aspects of compression molding, including its significance, operational procedures, utilized equipment and materials, applications, advantages, and a comparative analysis with injection molding.
What Is Compression Molding?
Compression molding is a manufacturing process that produces various plastic or composite parts. It is one of the oldest and most widely used methods of molding, dating back to the 19th century. It is especially suitable for processing thermosetting polymers, which are plastics that undergo irreversible chemical changes when heated and cured.
Compression molding can also be used to process thermoplastic compounds, which are plastics that can be melted and reshaped multiple times. However, thermoplastics are more commonly processed by injection molding, which offers higher production rates and lower material wastage.
Compression molding is an economical, time-tested solution for plastic fabrication. It can produce large, complex, and high-strength parts with minimal material wastage and low tooling costs. It can also accommodate various types of reinforcements, such as fibers or fillers, to enhance the mechanical properties of the final product.
How Does Compression Molding Work?
There are several steps involved in the compression molding manufacturing process. The first step is to create molds. These molds, typically made of steel or aluminum, are designed to meet dimensional and tonnage requirements. They consist of a cavity (space between the upper and lower mold) and an upper and lower mold as shown in Figure 1 below:
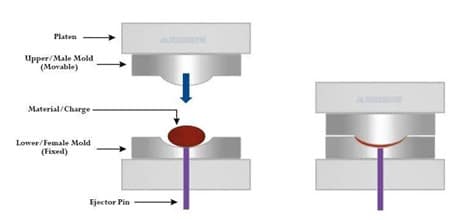
Next, the machine is set up for the molding process. The machine consists of a hydraulic press that applies pressure to the molds, a heating system that controls the temperature of the molds and the material, and a timer that regulates the cycle time.
The material to be processed is then prepared. The material can be in various forms, such as pellets, granules, sheets, or preforms. The material is preheated to a temperature below its melting or curing point, usually in an oven or on a hot plate. The preheating helps soften the material and reduce the cycle time.
The preheated material is then placed into the open mold cavity. The amount of material used depends on the size and shape of the part to be produced. The material should fill the cavity without overflowing or leaving gaps.
The mold is then closed, and high pressure is applied to compress the material and shape it to the desired form. The pressure can range from 5 to 200 MPa depending on the type of material and part. The pressure helps ensure that the material is evenly distributed and consolidated within the mold.
Heat is often used in conjunction with pressure to facilitate the curing or melting of the material. The combination of heat, pressure, and time causes the material to soften and flow, filling the mold cavities and taking on the desired shape. The curing process typically involves the material undergoing a chemical reaction, such as cross-linking, which gives it its final strength and durability.
Once the material has cured and solidified under pressure, the mold is opened, and the finished product is removed. The product may require some finishing operations, such as trimming, drilling, or painting, to improve its appearance and functionality.

Compression Molding Applications
Compression molding finds application in processing pre-impregnated intermediate products to create semi-structural and structural composite components. Recently, compression molding has been adopted for platelet-like materials, which are fiber strands or bundles pre-impregnated with a thermoset or thermoplastic matrix. These materials bear similarities to waste thermoset prepregs or recycled thermoplastic materials.
Compression molding also allows for the production of large complex composite components with minimal material wastage. It is an attractive option for numerous industries seeking robust and cost-effective manufacturing solutions.
The quality of parts produced through compression molding depends on several factors, such as material selection, mold design, process parameters, and quality control. Compression molded parts typically have high dimensional accuracy, surface finish, and mechanical properties. However, they may also have some defects, such as warping, shrinkage, flash, voids, etc. The life span of compression molded products depends on the type of material used and the environmental conditions to which they are exposed. Thermosetting polymers have high resistance to heat, chemicals, and wear and tear. They can last for several years without degrading. Thermoplastic compounds have lower resistance to heat and chemicals but can be recycled and reused.
Difference Between Compression Molding and Injection Molding?
Compression molding and injection molding are two of the most common methods of processing plastics. Both methods use heat and pressure to shape the material into the desired form. However, there are some significant differences between them in terms of the manufacturing process, materials used, and production rates.
The main differences between compression molding and injection molding are:
– In compression molding, the material is placed into an open mold cavity and then compressed by a press. In injection molding, the material is melted in a barrel and then injected into a closed mold cavity by a screw.
– Compression molding is better suited for thermosetting polymers that cure under heat and pressure. Injection molding is better suited for thermoplastic compounds that melt under heat and pressure.
– Compression molding can produce large, complex, and high-strength parts with minimal material wastage and low tooling costs. Injection molding can produce small to medium-sized parts with high precision and repeatability. – Compression molding has lower production rates than injection molding due to longer cycle times and manual loading and unloading of the material. Injection molding has higher production rates than compression molding due to shorter cycle times and automated feeding and ejecting of the material.
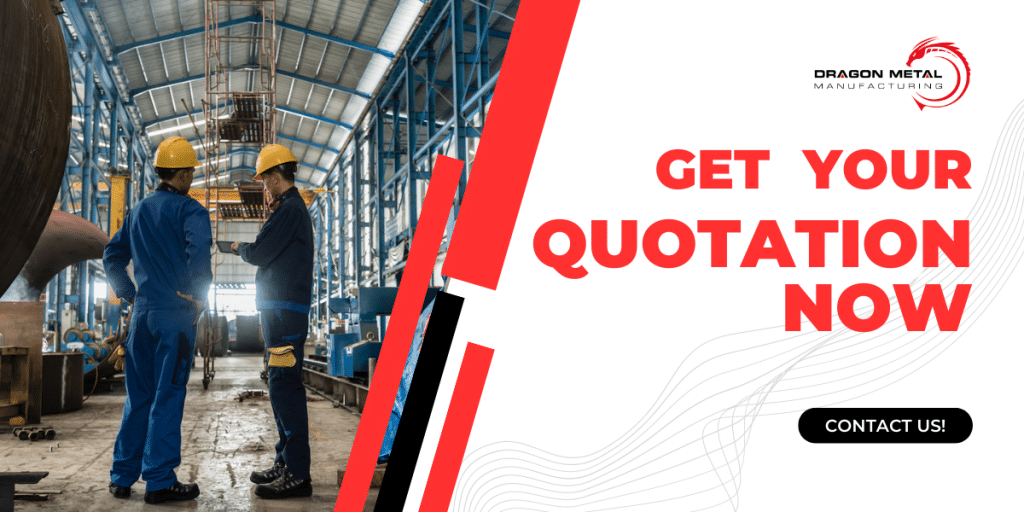
Conclusion
Compression molding is a manufacturing process used for creating plastic or composite parts by compressing preheated material into a mold cavity under high pressure. It’s renowned for its cost-effectiveness, enabling the production of large, intricate parts with minimal waste and low tooling costs. This method is widely employed across industries like automotive, aerospace, and consumer goods, offering versatility in accommodating various reinforcement types to enhance the final product’s mechanical properties.
Unlike injection molding, compression molding is ideal for thermosetting polymers that cure under heat and pressure, while injection molding suits thermoplastic compounds. Although compression molding excels in producing large, complex components with minimal material wastage, its production rates are slower due to longer cycle times and manual handling. In contrast, injection molding achieves higher production rates through automated processes, making it preferable for smaller, precision parts.