Manufacturing is a complex process that requires a well-structured and optimized approach. Designing for manufacturability is critical to the success of any manufacturing process, and it can be the difference between achieving shorter time to market – and therefore much lower costs, and a product stuck in a continuous research and development cycle, resulting in a heavy investment in terms of both time and money. In this article, we will discuss the best practices for design for manufacturing optimization that can help you substantially reduce your product development costs.
What is Design for Manufacturing (DFM)?
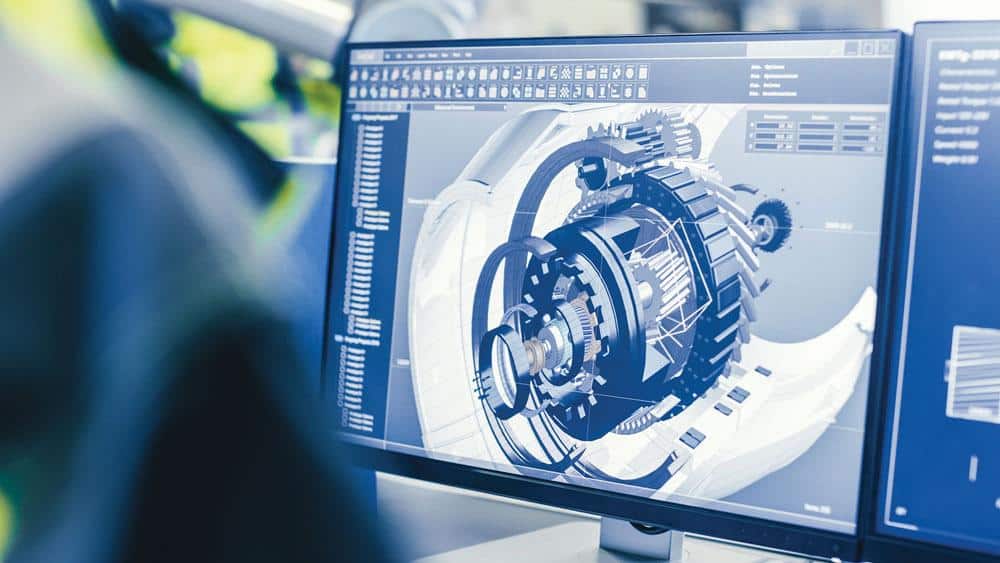
DFM is a systematic approach to designing products, which considers the manufacturing processes, the materials, the assembly, and even testing requirements. The goal of DFM is to minimize manufacturing costs and improve product quality. Designers should have a good understanding of the manufacturing processes and the capabilities and limitations of the manufacturing equipment and include this knowledge in the product design. In this way DFM reduces time to market and simplifies the manufacturing process.
When should Design for Manufacturing be Performed?
Design for Manufacturability should ideally be performed during the early stages of the product design process. It is best to start DFM as soon as possible, ideally during the conceptual design phase, in order to identify and address any potential manufacturing issues before they become too costly or time-consuming to fix.
How long does a DFM take?
The DFM process generally takes around two weeks to complete, but it can take longer depending on the complexity of the product. The process typically involves a series of steps, including design analysis, feedback and iteration, and final validation. The design team may need to perform multiple rounds of analysis and refinement to ensure that the design is optimized for manufacturing while still meeting the desired performance and functionality requirements.
Optimizing your Design for Manufacturing process
It is critical to optimize the DFM review for the following reasons:
Cost Reduction Designing a product with the manufacturing process in mind can significantly reduce manufacturing costs. It eliminates the need for expensive and time-consuming redesigns, and it ensures that the product is manufactured using the most cost-effective methods and materials.
Improved Quality Design for manufacturing ensures that the product is designed to meet the required quality standards. This is achieved by considering the manufacturing process, which helps identify potential quality issues early in the process.
Faster Time-to-Market Designing products for manufacturability can significantly reduce the time it takes to bring a product to market. It eliminates the need for lengthy redesigns, and it ensures that the product is manufactured using the most efficient production methods.
Best Practices for Design for Manufacturing Optimization
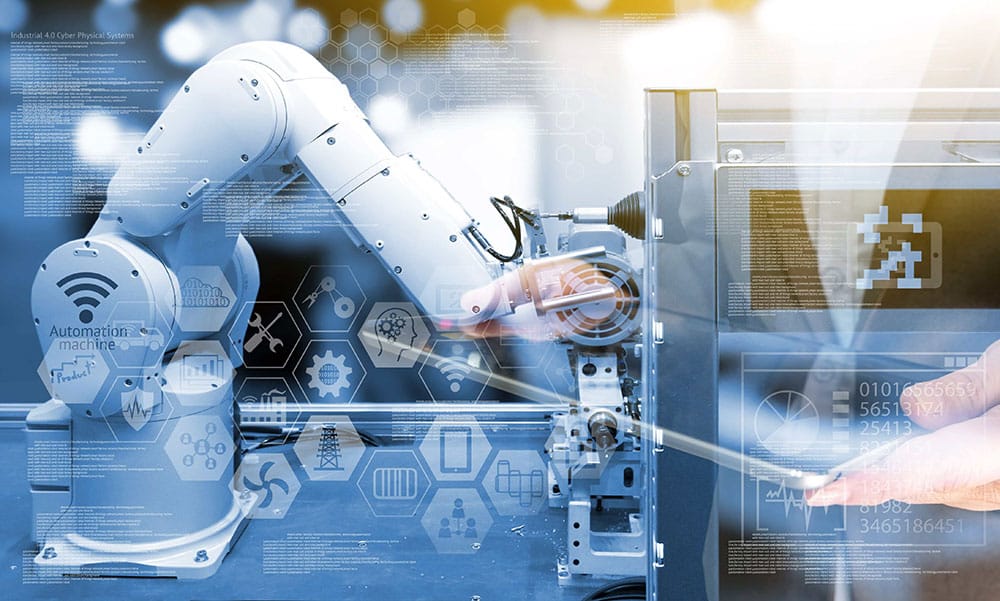
Involve Manufacturing Experts Early in the Design Process
To achieve optimal design for manufacturing, it is essential to involve manufacturing experts in the design process as early as possible. This helps ensure that the product is designed with the final manufacturing process in mind, and it can help identify potential manufacturing issues early in the design process.
Simplify the Design
Designs that are overly complex can be difficult and costly to manufacture. Discussing the design with your manufacturer and exploring ways to simplify the design can significantly reduce manufacturing costs and improve product quality.
Use Standard Materials and Components
Using standard materials and components can significantly reduce manufacturing costs. Standard materials and components are readily available, and they can be manufactured using well-established processes. For plastics, this means that the manufacturer will have more experience working with the material and within the necessary parameters resulting in a lot less unexpected issues.
Optimize Production Methods
Optimizing production methods can significantly improve the efficiency of the manufacturing process. This involves identifying the most efficient production methods and processes for each component and assembly process, every step of the way. During development, the first samples and production batch should generally use the same process that will be used for mass production, or at least make sure the product is designed with the end process in mind.
Implement Design for Assembly
Design for assembly involves designing products with the assembly process in mind. It involves simplifying the assembly process and minimizing the number of assembly steps required. This can significantly reduce assembly time and improve product quality while also saving assembly costs.
Conclusion
The Design for Manufacturing (DFM) approach involves considering various factors such as materials, production methods, and assembly processes. The primary goals are to minimize manufacturing costs, improve product quality and reduce the time it takes to bring a product to market. To achieve optimal design for manufacturing, it is essential to involve manufacturing experts early in the design process, simplify the design, use standard materials and components, optimize production methods, and implement design for assembly. By following these best practices, designers can create products that are efficient, effective, and cost-effective to manufacture.