Manufacturing has played a vital role in revolutionizing the healthcare industry, transforming it into a sophisticated and advanced sector. With the help of modern manufacturing techniques, medical devices, equipment, and drugs have become more accessible and affordable to people worldwide. In this article, we will explore how manufacturing revolutionized the healthcare industry, from the development of new drugs and medical equipment to the implementation of innovative technologies and production processes.
- The Evolution of Manufacturing in Healthcare
- Advancements in Medical Equipment Manufacturing
- The Role of 3D Printing in Medical Device Manufacturing
- The Growing Demand for Personalized Prosthetics and Implants
- The Future of Medical Manufacturing
- Importance of Quality Control in Healthcare Manufacturing
- Regulations in Healthcare Manufacturing
- Conclusion
The Evolution of Manufacturing in Healthcare
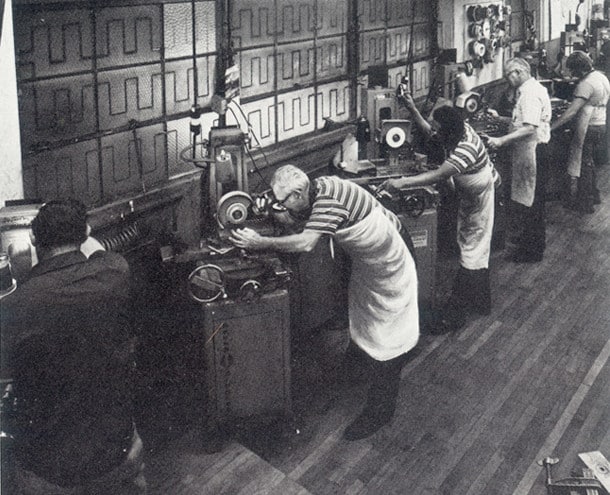
The healthcare industry has undergone significant changes since the 19th century, where medicine was less advanced, and medical equipment was less sophisticated. However, with the advent of the germ theory of medicine and the invention of the assembly line in the early 1900s, medical innovations became quicker, easier, and cheaper to produce. The 20th century saw the rise of automation and nanotechnology, which further enhanced what technology was able to accomplish for the human body.
As manufacturing techniques became more advanced, healthcare manufacturers started to use new technologies and processes to produce more efficient and affordable medical equipment, devices, and drugs. Personal medical devices, such as the artificial cardiac pacemaker, became a necessity, and the competition bred efficiency, resulting in higher quality products. Today, medical manufacturing companies focus on offering a vast array of products, from simple wound care equipment to advanced wearable medical technology, with a hallmark being the end-to-end management of their products. The heart of medical device manufacturing remains the same – a true desire to do good, strive for a healthier world, and make products that can truly help the public.
Advancements in Medical Equipment Manufacturing
Manufacturing revolutionized the healthcare industry by enabling the development of new and advanced medical equipment, such as MRI machines, CT scanners, and ultrasound machines. These machines have revolutionized the way doctors diagnose and treat diseases, enabling them to detect and treat diseases more effectively.
Moreover, manufacturing has enabled the development of smaller, more portable medical equipment, such as blood glucose monitors, that patients can use at home to monitor their health. This has given patients more control over their health and enabled them to manage their conditions more effectively.
The Role of 3D Printing in Medical Device Manufacturing
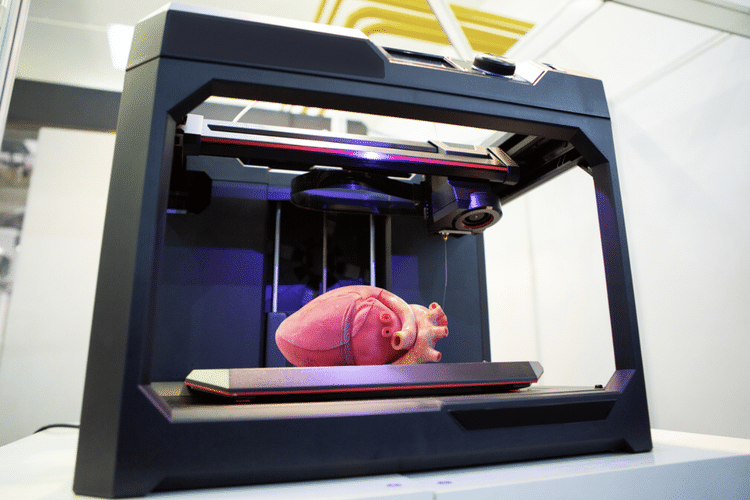
3D printing is another technology that manufacturing revolutionized the healthcare industry, particularly in the production of medical devices. 3D printing has made it possible to produce medical devices more quickly, accurately, and cost-effectively, enabling the development of:
- customized implants
- prosthetics
- and orthotics that are tailored to the patient’s unique needs.
Furthermore, 3D printing has made it possible to create more complex medical devices, such as heart valves, that were previously impossible to manufacture. This has led to significant advancements in the treatment of heart disease, enabling doctors to replace damaged heart valves with customized, 3D-printed versions.
The ability to create custom-made objects with precision and speed has opened up a range of possibilities for medical professionals. From creating patient-specific surgical models to 3D printing human organs, this technology has proved to be a game-changer for the healthcare industry. Here is the 5 Innovative Use Cases for 3D Printing in Medicine:
Patient-Specific Surgical Models
One of the most significant benefits of 3D printing in the medical field is the ability to create patient-specific surgical models. In the past, doctors relied on 2D imaging techniques like X-rays and CT scans to diagnose and treat patients. With 3D printing technology, doctors can create accurate 3D models of a patient’s anatomy, allowing them to practice complex surgeries before performing them on the patient. This reduces the risk of errors during the procedure and allows surgeons to improve their techniques. Additionally, 3D-printed surgical models can be used to train new surgeons and students, making the learning process more accessible and efficient.
New Medical Devices and Instruments
3D printing has also revolutionized the creation of new medical devices and instruments. In the past, creating a new medical device was a time-consuming and expensive process. With 3D printing technology, medical professionals can create prototypes and test new devices quickly and efficiently. Additionally, 3D printing allows for the creation of complex structures that would be impossible to manufacture using traditional techniques. This has led to the development of innovative medical devices like custom-made hearing aids, dental implants, and surgical instruments.
Affordable Prostheses
Traditionally, prostheses have been expensive and difficult to customize for individual patients. With 3D printing technology, it is now possible to create affordable and personalized prostheses. 3D printing allows for the creation of prostheses that are both functional and aesthetically pleasing. Additionally, 3D printing allows for the creation of prostheses that are lightweight and durable, making them more comfortable for patients to wear. This technology has the potential to transform the lives of people who have lost limbs due to injury or illness.
Corrective Insoles and Orthoses
Corrective insoles and orthoses are used to treat a variety of conditions, including flat feet, plantar fasciitis, and scoliosis. Traditionally, these devices were created using a plaster cast of the patient’s foot or body, which was then used to create a mould. With 3D printing, these devices can be created directly from a digital scan of the patient’s foot or body. This makes the process faster and more accurate, reducing the risk of errors. Additionally, 3D printing allows for the creation of lightweight and comfortable corrective insoles and orthoses, improving patient comfort and compliance.
Bioprinting, Tissue Engineering, 3D Printed Organs and Beyond The most ground-breaking application of 3D printing in medicine is bioprinting, tissue engineering, and the creation of 3D printed organs. Bioprinting is the process of creating three-dimensional structures using living cells. This technology has the potential to revolutionize the field of regenerative medicine by allowing for the creation of functional human organs for transplant. While the technology is still in its early stages, researchers have already used 3D printing to create functional liver tissue and miniature kidneys. In the future, bioprinting could be used to create organs on-demand, reducing the waiting times for transplant patients.
The Growing Demand for Personalized Prosthetics and Implants
Custom-made prosthetics and implants have increased due to the advancements in 3D printing technology and computer-assisted orthopaedic surgery. Standard implants cannot provide adequate solutions for non-traditional situations where patients’ bony geometries are outside the range of standard implant applications. Custom-made implants can be designed based on medical imaging with the use of specialized software packages, allowing images of the patient’s anatomy to be merged with computer-aided design models of corresponding implant systems.
In the case of bone defects, personalized implants can fit perfectly into the missing bone area and replace it. Traditionally these implants have been biologically inert but advancements are being made to replace these with bioactive materials. Biomechanical evaluation under patient-specific loading conditions allows for design modification prior to actual implant fabrication and application, reducing pain, recovery time, and enhancing osseointegration and function. Material selection may vary depending on the anatomical location, desired biomechanical strength, or need for biodegradability. Knowledge of anatomy, function, biomechanics, surgical approach, and material engineering is required for personalized implant design.
The use of personalized prosthetics and implants offers significant benefits in the field of orthopaedic surgery. With the help of advanced technologies such as 3D printing and computer-assisted surgery, surgeons can design and fabricate custom-made implants that perfectly fit the patient’s anatomy and biomechanics. This not only improves the surgical outcome but also reduces the risk of complications and promotes faster recovery. As these technologies continue to evolve, it is likely that we will see an increasing amount of crossover between AI and manufacturing capabilities. Think of Neuralink and their experiments aimed at enhancing human capabilities. We can already 3D print bionic eye prosthetics and print artificial skin and with these innovations accelerating over time, it will be very interesting to see what tomorrow brings.

The Future of Medical Manufacturing
These are just a few of the health innovations featured at CES 2023.
Virtual Reality Rehabilitation
A company called MindMaze is using virtual reality to help patients recover from injuries or neurological conditions. The technology can help patients regain physical function and cognitive abilities.
Wearable Health Sensors
Several companies are showcasing wearable devices that can monitor everything from heart rate and blood pressure to glucose levels and sleep patterns. These devices can help people stay on top of their health and catch potential health problems early.
Smart Inhalers
Companies like Propeller Health are using sensors and mobile apps to help people with asthma and COPD manage their conditions. The technology can track inhaler usage and remind patients when it’s time for their next dose.
AI-Powered Diagnostic Tools
Companies like Paige are using artificial intelligence to help diagnose diseases like cancer. The technology can analyse medical images and provide doctors with insights that can help them make more accurate diagnoses.
Mental Health Apps
Several companies are showcasing apps that can help people manage their mental health. These apps offer features like meditation exercises, mood tracking, and virtual therapy sessions.
Smart Beds
Sleep Number is showcasing a bed that can adjust to your body’s needs throughout the night. The bed uses sensors to track your heart rate, breathing, and movement, and can adjust the firmness and position of the mattress to help you get a better night’s sleep.
The future of medical manufacturing is rapidly evolving with the emergence of new technologies and processes that offer greater precision, efficiency, and adaptability. One of the most promising technologies is nanotechnology, which involves manipulating materials at the atomic and molecular level to produce ultra-small devices and drugs. Nanotechnology has the potential to revolutionize medical manufacturing by enabling the creation of more efficient and precise medical devices and drugs that can target specific cells or tissues in the body. This can lead to more effective treatments for a wide range of diseases and conditions.
In addition, the increasing use of data analytics and artificial intelligence in medical manufacturing is allowing manufacturers to optimize their production processes and develop new and innovative products more efficiently. By collecting and analysing data from various sources, including sensors, manufacturing equipment, and patient records, manufacturers can identify areas for improvement, predict equipment failures before they occur, and optimize production schedules to minimize downtime and reduce costs. Artificial intelligence is also being used to develop new materials and designs for medical devices, as well as to simulate the effects of drugs on the human body, accelerating the drug discovery and development process. With these technologies and processes, the future of medical manufacturing looks bright, with the potential for more effective treatments and faster, more efficient production processes.
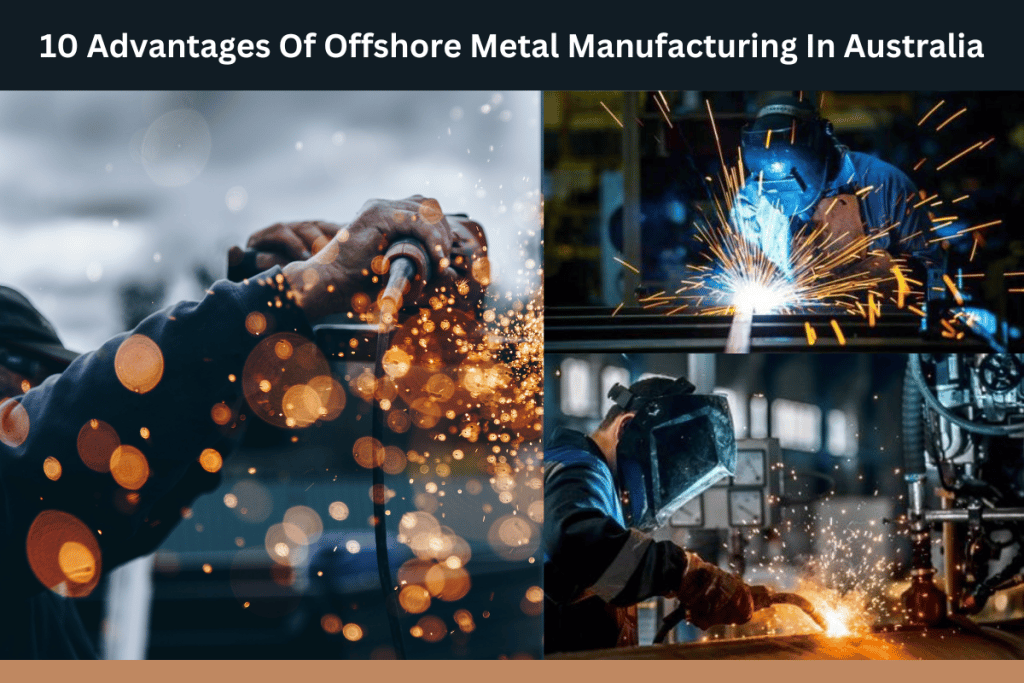
Importance of Quality Control in Healthcare Manufacturing
In healthcare manufacturing, ensuring the safety and efficacy of medical equipment, devices, and drugs is of utmost importance. This is where quality control comes in, as it involves rigorous testing and monitoring of products from raw materials to finished products, ensuring their quality and consistency. Quality control enables manufacturers to identify and address any quality issues that may arise during production, ensuring that products are safe and effective for patients.
Moreover, quality control plays a vital role in preventing errors in the manufacturing process that could lead to severe consequences. Medical devices are mainly used in the diagnosis, treatment, and rehabilitation following injury or disease, and any error in the manufacturing process could lead to a misdiagnosis, improper rehabilitation, or even death. Therefore, it is critical to have quality assurance programs in place to ensure that the highest standards of quality control are met.
For manufacturers that wish to develop and produce medical products, it is essential to get certified to ISO 13485. This is an internationally agreed standard that certifies that a manufacturer has quality management systems in place that are specific to the medical devices industry.
For manufacturing most medical devices, as well as drugs, it is essential to prevent cross-contamination. The best way to eliminate contamination and create a clean and controlled environment is to install a cleanroom. Cleanrooms are required to comply to ISO 14644, which sets limits to the amount of particulate matter that is allowed inside the controlled environment.
Regulations in Healthcare Manufacturing
Australia has stringent regulations for medical devices, and manufacturers must ensure their products meet specific standards before they can be sold in the country. In Australia, medical devices must be registered with the Therapeutic Goods Administration (TGA) and comply with the Australian Therapeutic Goods (Medical Devices) Regulations 2002. To obtain TGA approval, manufacturers must provide evidence of the safety, quality, and performance of their products through clinical trials and other testing procedures.
Additionally, medical devices must meet specific labelling requirements and carry appropriate warnings to ensure user safety. Products that have already received CE certification in Europe may have an easier time obtaining TGA approval, as the standards are similar. It is important for manufacturers to understand and comply with these regulations to ensure their products are legally marketed in Australia.
Conclusion
Manufacturing has played a crucial role in the transformation of the healthcare industry, from the production of medical devices to the development of life-saving drugs. Advanced technologies and modern manufacturing techniques have enabled manufacturers to create innovative products that meet the highest standards of safety, while also reducing costs and increasing efficiency. The future of healthcare manufacturing looks promising, with digital technologies like blockchain and IoT expected to enhance the efficiency and safety of manufacturing processes. Overall, how the manufacturing revolutionized the healthcare industry has improved the quality of care for patients and transformed the way healthcare is delivered and consumed.
Contact us today to learn more about our offshore manufacturing capabilities and how we can help you produce innovative medical devices at an affordable cost.