In today’s fast-paced business world, manufacturers are continuously seeking ways to enhance their production processes and remain competitive. One such approach that has gained popularity in recent years is lean manufacturing. Lean manufacturing is a systematic approach to identifying and eliminating waste in the production process while also improving efficiency, quality, and delivery times. In this article, we will delve into the world of lean manufacturing, exploring its history, principles, implementation strategies, benefits, and challenges. We will also discuss some of the commonly used lean manufacturing tools and how they can be applied to your production processes.
Table of Contents
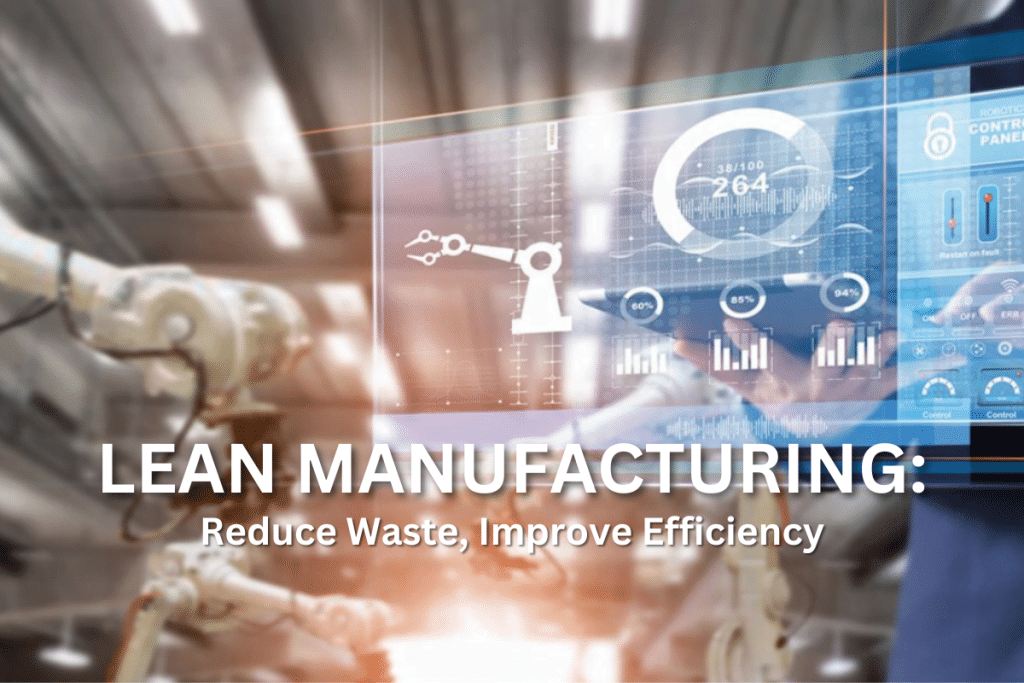
What is Lean Manufacturing?
Lean manufacturing is a systematic approach to minimizing waste and maximizing value by optimizing the flow of materials, products, and information through the production process. This approach involves identifying and eliminating non-value-added activities, such as overproduction, excess inventory, defects, waiting, unnecessary processing, unnecessary motion, and unused talent.
The goal of lean manufacturing is to create a lean culture that emphasizes continuous improvement, employee involvement, and customer satisfaction. It is a holistic approach that involves everyone in the organization, from the shop floor to the executive suite.
The Five Principles of Lean Manufacturing
There are five core principles of lean manufacturing that guide the implementation of the approach. These principles are:
Value
The first principle of lean manufacturing is to focus on the customer and the value they receive from the product or service. This involves understanding what the customer wants and needs and designing the production process to deliver that value.
Value Stream
The second principle of lean manufacturing is to identify and map the value stream, which is the series of activities that transform raw materials into finished products. This involves understanding the flow of materials, products, and information through the production process and identifying any non-value-added activities or waste.
Flow
The third principle of lean manufacturing is to create a continuous flow of materials and products through the production process. This involves removing any bottlenecks, optimizing the flow of work, and ensuring that materials and products move seamlessly from one process to the next.
Pull
The fourth principle of lean manufacturing is to implement a pull system, where products are only produced when they are needed. This involves setting up a system that responds to customer demand and produces only what is needed, when it is needed, and in the amount needed.
Perfection
The fifth and final principle of lean manufacturing is to strive for perfection by continuously improving the production process. This involves empowering employees to identify and eliminate waste, implementing continuous improvement processes, and using data and metrics to drive decision-making.
Implementing Lean Manufacturing
Implementing lean manufacturing involves a series of steps, including identifying waste, creating a lean culture, continuous improvement, and using lean tools and techniques.
Identifying Waste
The first step in implementing lean manufacturing is to identify waste in the production process. Waste can be categorized into seven types, including overproduction, excess inventory, defects, waiting, unnecessary processing, unnecessary motion, and unused talent.
Once waste has been identified, the next step is to eliminate it through a series of targeted improvement efforts. This may involve reorganizing workspaces, streamlining processes, and automating certain tasks.
Creating a Lean Culture
Creating a lean culture involves developing a shared mindset and set of values that prioritize continuous improvement, employee involvement, and customer satisfaction. This may involve training employees on lean principles and encouraging them to participate in improvement initiatives.
Continuous Improvement
Continuous improvement is a core aspect of lean manufacturing and involves a cycle of planning, doing, checking, and acting to drive ongoing improvement in the production process. This may involve implementing kaizen events, which are short-term improvement initiatives focused on a specific process or problem.
5 Common Lean Tools and Techniques
There are several tools and techniques that can be used to support the implementation of lean manufacturing, including:
Value Stream Mapping: A tool used to visualize and analyse the flow of materials and information required to bring a product or service from its initial state to the customer. It helps identify inefficiencies and waste in the process and provides a roadmap for improvement.
5S: A methodology for organizing and improving the workplace by implementing five principles: Sort (separating necessary items from unnecessary), Set in Order (arranging necessary items for easy access), Shine (cleaning and inspecting the work area), Standardize (establishing consistent practices), and Sustain (maintaining the improvements).
Kaizen: A philosophy of continuous improvement, focused on making incremental changes to processes and systems to eliminate waste and increase efficiency. It involves the participation of all employees in identifying and implementing improvements.
Gemba: A Japanese term meaning “the real place.” In Lean, it refers to the place where the work is being done, such as a factory floor or customer service centre. It emphasizes the importance of going to the source to observe and understand the work processes in order to identify opportunities for improvement.
Kanban: A visual system for managing workflow and inventory, using cards or other signals to signal when new items are needed and when work can begin on a new task. It helps prevent overproduction and ensures that work is pulled through the system only as needed, reducing waste and improving efficiency.
Benefits of Lean Manufacturing
Incorporating the principles of lean manufacturing in your processes can enhance your productivity by making value flow effortlessly at the pull of the customer, which is also known as Just in Time (JIT). The implementation of lean techniques not only helps prevent waste but can also eliminate it.
There are seven categories of waste: Transport, Inventory, Motion, Waiting, Over-processing, Overproduction, and Defects. Each waste type has a direct impact on your expenses, as they do not add any value to the final product or service that you provide to your customers. These non-value-adding operations are not something your customers would be willing to pay for, making it essential to eliminate them from your processes.
Studies have shown that typically only 5% of the time spent in operations adds value, while the remaining 95% is considered waste. Imagine the impact on your operations if you could remove this wasted time and effort. It would be significant!
Implementing Lean manufacturing techniques can improve various aspects of your operations, including quality performance by reducing defects and rework, both in-house and at the customer level. It also leads to fewer machine and process breakdowns, lower inventory levels, higher stock turnover, less space required, and higher efficiencies, resulting in more output per man-hour.
Incorporating lean techniques in your processes can also lead to improved delivery performance, faster development, greater customer satisfaction, improved employee morale and involvement, improved supplier relations, higher profits, and increased business. These benefits are all compelling reasons to implement Lean techniques in your operations.
Challenges of Lean Manufacturing
Implementing lean manufacturing can also present a range of challenges, including:
Resistance to change: Implementing lean manufacturing often involves significant changes to the production process, which can be met with resistance from employees.
Initial costs: Implementing lean manufacturing may require significant investments in new equipment, training, and other resources.
Difficulty sustaining improvements: Continuous improvement is a core aspect of lean manufacturing, and sustaining improvements can be a challenge. It requires ongoing monitoring and adjustment to ensure that the production process remains lean and efficient.
Conclusion
Lean manufacturing is a production philosophy that prioritizes efficiency, waste reduction, and continuous improvement. By implementing lean principles and techniques, manufacturers can reduce costs, improve product quality, and increase customer satisfaction. However, implementing lean manufacturing can also present challenges, including resistance to change and the initial costs of implementation. To successfully implement lean manufacturing, manufacturers must create a culture of continuous improvement and be willing to invest in the resources necessary to sustain it.