Laser cutting is a popular and versatile method of cutting metal into precise shapes and sizes. Laser cutting can produce complex and intricate designs with high accuracy and efficiency. But how does laser cutting work, and what are the different types of lasers and metal materials used in this process? In this blog post, we will answer these questions and more.
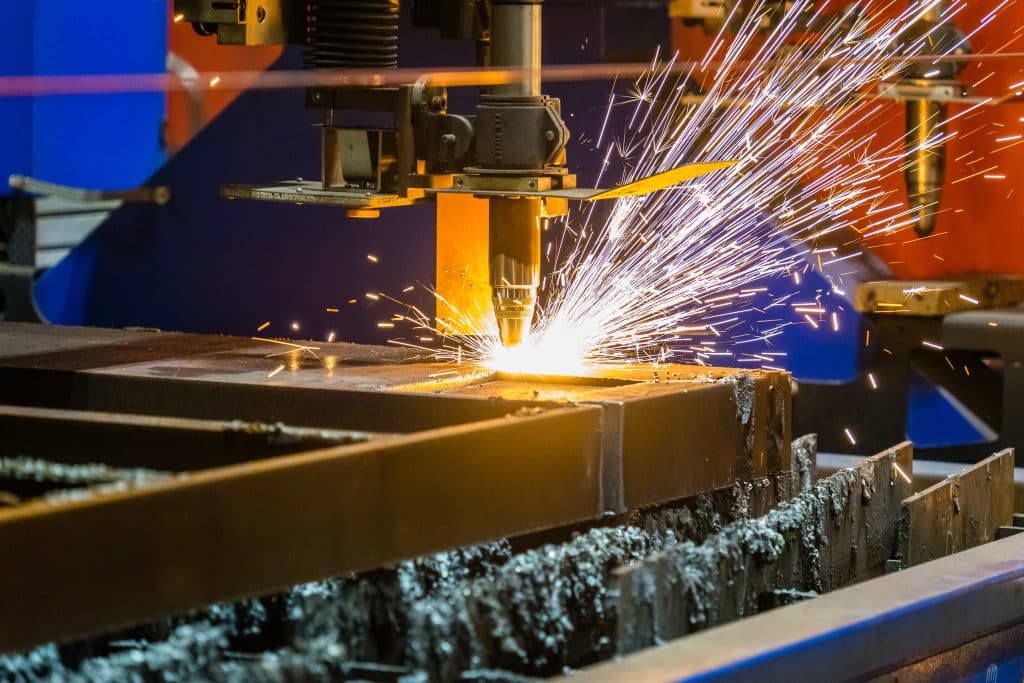
What is Metal Laser Cutting?
Metal laser cutting is a process that uses a focused beam of light to cut or engrave metal. The laser beam heats up the metal until it melts or vaporizes, creating a clean and smooth cut. The laser beam can be controlled by a computer program or a manual operator, depending on the type of machine and the desired outcome.
Brief History of Metal Laser Cutting
The first laser cutting experiments were conducted in 1965 at the Western Electric Engineering Research Center, where researchers used a laser to drill holes in diamond dies. A few years later, they developed a new method of laser cutting using carbon dioxide, which made the process more versatile and efficient. Carbon dioxide lasers could cut through different types of materials, including metals.
The aerospace industry was one of the first to adopt laser cutting as a commercial application. In 1969, Boeing published a paper describing how they used a carbon dioxide laser to cut titanium, Hastelloy, and ceramic for their aircraft components. They also introduced the concept of multi-beam laser cutting, which increased the productivity and accuracy of the process. Boeing started using laser cutting on their production lines as a reliable and cost-effective method.
In the 1970s, Western Electric mass-produced laser cutting machines that were widely used in the aerospace sector and other industries. Laser cutting became more popular and accessible as the technology improved and the costs decreased.
In the 1980s, gas laser cutting was widely used for cutting metals like mild steel. It is estimated that there were 20,000 industrial laser cutters in operation by the end of the decade. Laser cutting revolutionized the manufacturing industry and paved the way for a new era of innovation.
In 1979, Prima Industrie of Italy invented a 3D laser cutting process that expanded the possibilities of laser cutting technology. 3D laser cutting allowed for more complex and precise shapes and designs to be created with lasers. Today, laser cutting is used in various sectors, such as automotive, medical, and art.
Laser cutting is a remarkable technology that has evolved over time and continues to advance. It is a powerful tool that can create amazing products and solutions for various needs and applications.
How does Metal Laser Cutting Work?
Metal laser cutting involves two main steps: prep work and cutting. Let’s take a look at each step in detail.
Prep Work before Metal Laser Cutting
Before the actual cutting process, the metal material needs to be prepared for the laser. This may include cleaning, coating, marking, or positioning the metal on the machine. The type and extent of prep work depend on the type of metal, the type of laser, and the desired result.
How to Laser Cut Metal
The actual cutting process involves directing a focused laser beam onto the metal surface. The laser beam can be moved along a predetermined path or guided by a manual operator. The laser beam melts or vaporizes the metal along the cut line, creating a kerf (a narrow gap). The melted or vaporized metal is then blown away by a gas jet, leaving behind a clean and smooth cut edge.
What Metal Material Can Be Laser Cut?
Laser cutting can be used to cut various types of metal materials, such as:
Stainless Steel
Stainless steel is a popular choice for laser cutting because of its high corrosion resistance, durability, strength, weather resistance, and suitability for outdoor use. It also contains nickel, which makes it easier to cut than mild carbon steel. It can achieve smooth edges and small radius cutouts. Stainless steel is widely used in industries that require high-quality finishes.
Aluminium
Aluminium is a lightweight metal that can be efficiently laser cut. Some non-heat treatable grades, such as 5052 and 6061, are commonly laser cut. However, aluminium is highly reflective, which allows faster cuts but also causes oxidation on the cut edges. This metal is used for electronic enclosures, aerospace structures, automotive, and consumer electronics.
To prevent scratches on aluminium during laser cutting, it is advisable to avoid sharp edges and hard friction on the material surface. Applying a clear lacquer or light oil on the surface can also protect the surface. Scratches on the backside of the sheets can be easily removed with a light abrasive.
Titanium
Titanium is a difficult metal to cut, but laser cutting can achieve precise and intricate cuts. Titanium has high strength and lightweight properties, which make it ideal for aerospace, medical, marine, and automotive applications.
Copper
One of the most common metals in electrical and plumbing applications is copper, thanks to its high electrical conductivity. Copper can be cut with lasers, but it may require more powerful machines because of its high thermal conductivity. To avoid discoloration, fibre lasers are recommended. Copper laser cutting is useful for making electrical contacts and heat exchangers.
Types of Lasers Used in Metal Laser Cutting
There are three main types of lasers used in metal laser cutting:
CO2 lasers
CO2 lasers are gas lasers that use carbon dioxide as the lasing medium. CO2 lasers have a wavelength of 10.6 micrometres, which makes them suitable for cutting most metals. CO2 lasers have high power output and efficiency, but they also require high maintenance and cooling costs.
Fiber lasers
Fiber lasers are solid-state lasers that use optical fibres as the lasing medium. Fiber lasers have a wavelength of 1.06 micrometres, which makes them ideal for cutting reflective metals such as aluminium, copper, or brass. Fiber lasers have lower power consumption and maintenance costs than CO2 lasers, but they also have lower beam quality and stability.
Nd and Nd:YAG lasers
Nd and Nd:YAG lasers are solid-state lasers that use neodymium-doped crystals as the lasing medium. Nd and Nd:YAG lasers have a wavelength of 1.06 micrometres, which makes them similar to fibre lasers in terms of metal cutting capabilities. Nd and Nd:YAG lasers have higher beam quality and stability than fibre lasers, but they also have higher power consumption and maintenance costs.
Methods Used in Laser Cutting Processes
There are five main methods used in laser cutting processes:
- Vaporization cutting: Vaporization cutting is a method that uses high-power laser beams to heat up the metal until it vaporizes, creating a large kerf. Vaporization cutting is suitable for cutting thin and non-metallic materials, such as wood, plastic, or paper.
- Reactive cutting/ Flame cutting: Reactive cutting is a method that uses oxygen as the assist gas to create an exothermic reaction with the metal, increasing the cutting speed and efficiency. Reactive cutting is suitable for cutting thick and carbon-rich metals, such as mild steel or carbon steel.
- Melt and blow cutting/ Fusion cutting: Melt and blow cutting is a method that uses nitrogen or argon as the assist gas to blow away the molten metal, creating a narrow kerf. Melt and blow cutting is suitable for cutting thin and non-oxidizing metals, such as stainless steel or aluminium.
- Thermal stress cracking cutting: Thermal stress cracking cutting is a method that uses low-power laser beams to create thermal stress cracks on brittle materials, such as glass or ceramics. Thermal stress cracking cutting is suitable for cutting complex and delicate shapes on fragile materials.
- Stealth dicing cutting of silicon wafers: Stealth dicing cutting of silicon wafers is a method that uses ultra-short laser pulses to create micro-cracks inside the silicon wafer, separating it into smaller pieces. Stealth dicing cutting of silicon wafers is suitable for cutting thin and sensitive materials, such as semiconductor chips or solar cells.

Applications of Laser Cutting
Laser cutting is a versatile technology that can be applied to various domains and purposes. Here are some examples of how laser cutting is used in different fields:
Industrial Uses
Many industries rely on laser cutting to produce parts that need high accuracy and quality, such as metal sheets, pipes, tubes, gears, brackets, flanges, fittings, valves, implants, instruments, tools, moulds, and dies. These industries include manufacturing, aerospace, medical, automotive, engineering, construction, and more. Laser cutting is ideal for these sectors because it can cut complex shapes and patterns with speed and precision.
Artistic Applications
Laser cutting is also a great tool for artistic expression and creation. It can be used to make or improve various artworks that need creativity and aesthetics, such as sculptures, accessories, jewellery, and more. These artworks can be found in design, architecture, fashion, jewellery, crafts, decorations, and more. Laser cutting allows artists to explore different materials and styles with ease and flexibility.
Personal Uses
Laser cutting is not only for professionals and artists. It is also available for hobbyists, enthusiasts, students, teachers, and more. They can use laser cutting to make or enjoy various personal projects that need fun and learning, such as toys, models, games, educational kits, science experiments, and more. Laser cutting is a fun way to learn about science, technology, engineering, art, and math (STEAM).
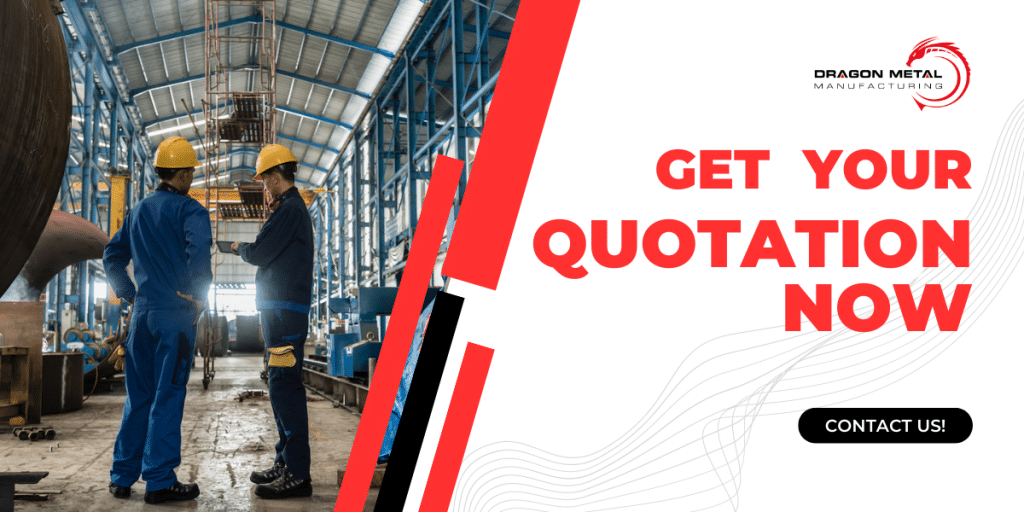
Conclusion
Laser cutting is a versatile and efficient method of cutting metal into precise shapes and sizes. Laser cutting can use different types of lasers and metal materials, depending on the desired outcome. Laser cutting can also use different methods of cutting processes, depending on the type and thickness of the material. Laser cutting has many applications in various industries, from aerospace to art. Laser cutting is a technology that continues to evolve and improve, offering new possibilities and opportunities for metal fabrication.