The industrial sector relies heavily on metal fabrication materials and its technologies to meet its operational requirements. Today, an extensive range of metals and their respective alloys are used to fabricate industrial components across the industrial sector. These metals are chosen according to crucial industry-specific factors that include tensile strength, formability, weight, resistance to corrosive agents, and cost considerations. Within this extensive range of materials is an exclusive group of common metals used in fabrication.
Common Metal Fabrication Materials
The following are the common metals used in metal fabrication:
- Stainless Steel – This refers to the group of steels with very low corrosion rates, allowing them to be used in environments with corrosive agents such as moisture. Stainless steel can be categorised into five grade types:
- Austenitic – The austenitic grade of stainless steel provides manufacturers with a highly corrosion-resistant, temperature-resistant, and durable material for fabricating parts. Examples include the SS 200 and 300 series used in manufacturing packaging and domestic appliances.
- Ferritic – Ferritic steel is covered under series 400 stainless steel and is defined by a body-centred cubic grain structure, with concentrations of carbon and chromium. Some ferritic steel examples in SS 400 family include SS 409, 430, and 439 grades used in the automotive and industrial manufacturing industries.
- Martensitic – Martensitic steel is designed to have extensive tensile strength and wear resistance. It may be ferromagnetic, just like ferritic steel. The common types of martensitic steel fall within the stainless steel series 400 and they include 410, 420, and 440A grades.
- Duplex – This category consists of stainless steel structures with a two-phase microstructure that includes both ferritic and austenitic properties. Examples of Duplex stainless steel include Duplex alloys 2507, 2304, and 2550 used in the oil and gas industry and in paper production.
- Precipitation Hardening Steel – These are highly corrosion-resistant steel grades that fall under the 304 stainless steel categorisation. Examples include stainless steel 304, 310, and 316. Precipitation hardening steel is used in manufacturing industrial engineering products such as gears, valves, and other engine components.

2. Mild Steel – Mild steel is a commonly fabricated metal used in various industries including construction, automotive, plumbing, and many more. It is a type of low-carbon steel where carbon content depends on the steel requirement. Mild steel is highly machinable and has overall impressive physical properties including high impact and tensile strength, good malleability, and weldability.
Hot rolling and cold rolling are processes that lead to two different sets of properties for each type of steel to be fabricated. Hot-rolled steel is easier to fabricate due to its malleability when heated to temperatures above 900°Celsius. Cold-rolled steel is also heated to high temperatures and then left to cool at room temperature before it is formed. This means cold-rolled fabricated parts are typically harder than hot-rolled fabricated components.
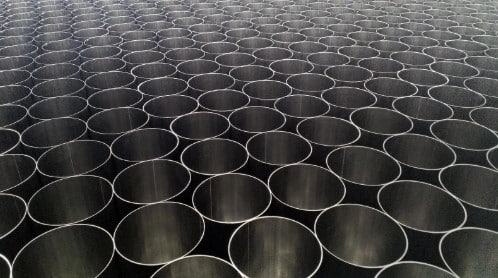
3.Aluminium – The use of aluminium in metal fabrication is common across the fabrication and manufacturing industry. Aluminium brings extensive properties to the table, such as easy malleability, corrosion resistance, temperature resistance, compatibility with other metals, and the option of using a multitude of aluminium alloys.
Aluminium is obtained from bauxite. Diverse fabrication techniques including metal stamping and welding may be applied to create the desired forms. Aluminium’s most endearing property is its strength-to-weight ratio, which means it offers extensive durability at lesser weights compared to other metals such as stainless steel. This feature makes it the go-to metal fabrication material in the automotive and aerospace industries. You can learn more about aluminium fabrication techniques here.
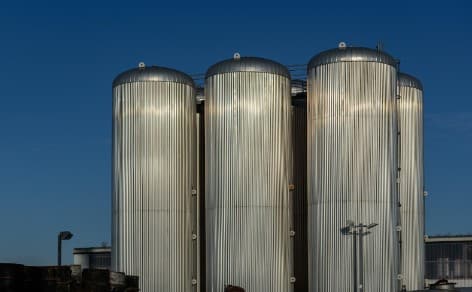
4. Brass – The manufacturing industry relies on brass fabrication to produce fixtures and fittings across the healthcare, consumer goods, domestic, and entertainment industries. Brass is an alloy consisting of copper and zinc in varying degrees. Its popularity as a metal fabrication material is due to its mechanical and electrical properties, resistance to bacteria, high levels of strength, and malleability.
Fabrication techniques such as casting, cutting, and punching are used to form brass into finished items or end-use parts.
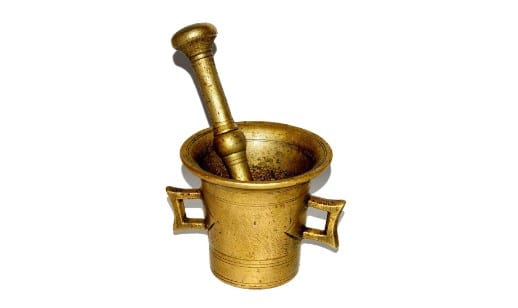
5. Copper – Purified copper is commonly used in manufacturing due to its ductility, resistance to corrosion, resistance to bacteria, and excellent thermal and electrical conductivity. Copper fabrications are used within the electrical engineering industry, precious metal industry, construction industry, and cooling systems.
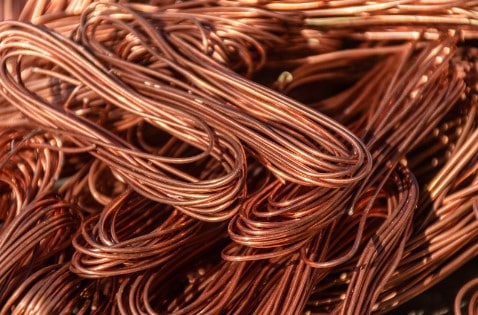
Fabricating these common metals requires the expertise of a fabricator using the right tools and machinery to produce high-performing metal parts. You can learn more about metal fabrication for your industry-specific requirements by speaking to the experts today. Contact a Dragon Metal Representative.