Imagine you’ve conceived a brilliant new product idea that you’re eager to unveil to the world. Whether you’re an independent inventor or representing a sprawling multinational enterprise, the path to introducing a novel product can prove to be a formidable journey. Even seasoned industry professionals are not immune to the challenges that come with this endeavor. Join us in exploring how to optimize your production process, transforming a promising prototype to production.
Our mission is to simplify this entire voyage – from the initial stages of prototyping to the final phases of production. Our approach centers around sharing valuable insights from a manufacturer’s perspective. With our accumulated knowledge, we are confident that your expedition towards a triumphant product launch can be streamlined, sparing you precious time, financial resources, and the vexations that often accompany such ventures.
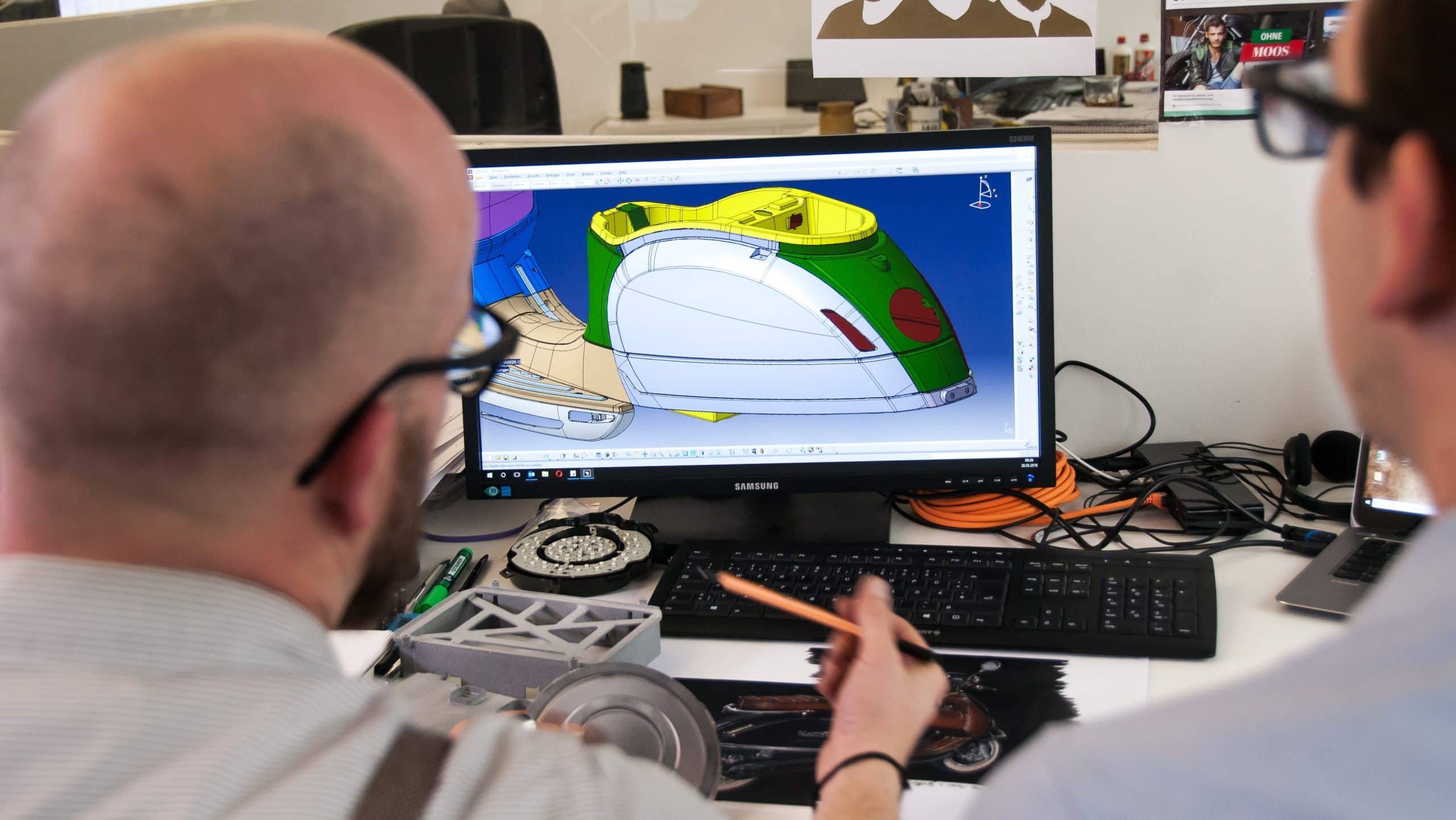
Understanding the Prototyping Stage
Significance of Prototyping in Product Development
Prototyping stands as the bridge between ideation and realization, providing a tangible manifestation of creative visions. For instance, when Apple introduced the iPhone, they underwent several prototyping iterations to fine-tune the device’s design, user interface, and functionality. Each prototype iteration brought them closer to a groundbreaking product that would reshape the mobile industry. Similarly, Tesla’s Model 3 underwent rigorous prototyping, allowing the company to perfect its electric vehicle technology and accelerate the transition to sustainable transportation.
Benefits of Testing and Refining Product Design
At its core, prototyping enables iterative testing and refinement of product designs. By subjecting prototypes to real-world scenarios, potential design flaws surface, and valuable insights emerge. Consider the case of Dyson, a pioneer in vacuum cleaner technology. Dyson’s engineers created over 5,000 prototypes for their revolutionary bagless vacuum, refining aspects like suction power, dust separation, and usability. This relentless testing and optimization culminated in a product that transformed an entire industry and set new standards for performance.
Gathering Feedback from Stakeholders
Prototyping serves as a conduit for engaging stakeholders, nurturing collaboration, and actively soliciting feedback. A compelling example of this lies in Boeing’s development of the 787 Dreamliner. By creating early-stage prototypes of cabin layouts and amenities, Boeing engaged airlines to gather insights that shaped the passenger experience. This iterative process not only optimized passenger comfort but also aligned with airlines’ operational needs, culminating in a product that redefined air travel.
In the realm of manufacturing, General Electric (GE) harnessed the power of prototyping when designing their advanced gas turbines. Through prototyping, GE engaged energy providers to test turbine performance under real-world conditions. This dynamic feedback loop led to refinements in turbine efficiency and durability, ultimately bolstering energy generation capabilities and solidifying GE’s position as an industry leader.
Prototypes don’t merely represent a stage in development; they serve as dynamic interfaces for collaboration, nurturing a partnership between creators and stakeholders that drives innovation forward.
The Prototype to Production Process Demystified
Investing in Design Drawings for Production Success
The bedrock of a triumphant production endeavor resides in meticulous design drawings. If you wield proficiency in design software, you can undertake this task, ensuring precision and finesse. Design drawings, whether in 2D blueprints or 3D models, serve as comprehensive documents that encompass dimensions, tolerances, surface finishes, and other critical details. They also facilitate seamless communication with manufacturers and enable the programming of digital manufacturing machines. For those lacking design acumen, enlisting a professional consultancy can prove invaluable. The design stage represents a pivotal juncture where potential errors can be discerned and rectified most efficiently and cost-effectively.
Keeping it Simple for a Streamlined Production Process
The age-old adage of “simplicity is key” reverberates profoundly in the realm of manufacturing. Advocating for streamlined designs is not a mere suggestion; it’s a strategy rooted in efficiency and cost-effectiveness. Simplified designs expedite manufacturing, curtail expenses, and capitalize on standardized materials that are both accessible and economical. With each added layer of complexity, costs escalate, production timelines elongate, and the risk of errors or rejected components magnifies. Furthermore, in scenarios where a project might prove unfeasible, a simple design mitigates financial exposure.
Avoiding Tight Tolerances to Minimize Manufacturing Challenges
Striking a balance between precision and pragmatism is a tenet that underscores successful production. While achieving ultra-tight tolerances is possible, it often comes at a steep cost in terms of time, effort, and resources. Moderation in dimensional tolerances is a prudent approach for most designs, allowing for efficient manufacturing without compromising functionality. For instance, in CNC machining, a tolerance of +/- 0.05mm is readily attainable and more than adequate for the majority of consumer and industrial components. Imposing stricter tolerances entails heightened complexity, increased expenses, and a higher likelihood of rejects, all without commensurate gains in performance or aesthetics.
Creating a Bill of Materials for Efficient Production
It is a good practice to create a BOM for your product from the prototyping stage as this will clearly state all the component details as well as specifying who makes what, this becomes a pivotal requirement as you transition to full-scale from prototype to production. Each element within the assembly, down to the minutest detail like nuts, bolts, screws, and adhesives, must be meticulously accounted for. A comprehensive BOM empowers meticulous cost assessment, a crucial consideration especially when scaling up to large volumes. By preemptively addressing every component’s cost, you effectively manage expenditures and foster a more streamlined supply chain.
Choosing the Right Materials and Surface Finishes
Opting for the appropriate materials and surface finishes is an art that significantly impacts the production journey. The selection of materials should align with practicality and scalability rather than ostentation. While prototypes might showcase exotic materials for showcase purposes, high-volume manufacturing thrives on readily available and cost-efficient raw materials. Such substitutions expedite procurement and leverage manufacturers’ expertise, thereby ensuring consistent outcomes. Similarly, while prototypes may boast elaborate surface finishes, large-scale production demands efficiency. Employing an “as machined” surface finish for non-cosmetic parts strikes an optimal balance between aesthetics and practicality. For cosmetic surfaces, techniques like painting, plating, or anodizing can confer durability and visual appeal without compromising efficiency.

Tips for Moving from Prototype to Production
Finding a prototyping specialist for fidelity and expertise
Bringing in a prototyping specialist is like having a skilled coach on your team. The process of making prototype to production can be quite different from mass production. It’s not just about the machines – it involves paying close attention to details and being flexible with materials and methods, something not all factories are set up for when dealing with small custom orders. Product Designers and mechanical engineers understand that it may take weeks to fine tune their designs. So they often try to work with a manufacturer who can quickly help them prove their concept with a physical sample to test and validate.
Selecting the appropriate manufacturing process
There are many manufacturing processes to choose from for your product. Choosing the right way to make your prototype is a bit like selecting the best tools for a job. When it comes to metal prototypes, you’ve got a few options. CNC machining, which involves carving out pieces from metal or plastic, is versatile and quick. It’s like sculpting a detailed model out of clay. Metal stamping, on the other hand, is more like shaping metal into specific forms, often used for flat or thin parts. Then there’s 3D metal printing, which can create really complex shapes, although it’s a bit trickier to work with. If you’re making prototypes from plastic, you can go for CNC machining, polyurethane vacuum casting, or 3D printing, each with its own pros and cons.
Sculpting Success: Transitioning from CNC Prototyping to Production
Moving from making prototype to production is a bit like scaling up a recipe for a big dinner party. If you started with a small batch and now need to make a lot more, you might tweak the cooking method or use bigger pots and pans. Similarly, when transitioning from CNC prototyping to production, some adjustments might be made to the machining process or tools to increase efficiency. This shift is all about finding ways to make things faster and more cost-effective while keeping the quality high.
Planning for certification and testing in the prototyping phase
Unlike testing a single dish in your kitchen, making products for the market sometimes involves meeting certain safety and quality standards. It’s like getting your recipe approved by a panel of food critics before you can serve it to the public. Depending on the product it may be necessary to go through certification processes to ensure they meet various regulations. Just as a dish needs to be tasted and tested multiple times before it’s ready to be served to guests, your products need to be rigorously tested and certified before they hit the market.
Conclusion: Paving the Way to Successful Production
Getting your product right can take a very long time and your design may need to undergo many iterations before you are ready for production. One suggestion for shortening your time to market is to consult with a production manufacturer, who can advise whether your design can be scaled up for production. Knowing your product is fit for manufacturing allows you to focus on the essential steps that will achieve your product in the most cost-effective and efficient way.
Are you ready to take your idea to the market? If you’re looking for a reliable partner to help you optimize your production, look no further. Dragon Metal Manufacturing is here to provide top-quality solutions for your manufacturing needs. Let us join you in turning prototypes into real products, backed by a commitment to quality that matches your own.