Laser cutting has reformed the field of metal fabrication, enabling precise and intricate cuts in a wide range of materials. With its unparalleled accuracy and versatility, laser cutting has become a preferred method for creating complex designs and achieving high-quality results. This technology utilizes the power of a focused laser beam to vaporize or melt the material, providing a clean and precise cut without the need for physical contact. In this article, we will explore the intricacies of laser cutting its precision capabilities, advantages in metal fabrication, factors affecting precision, and future trends in this rapidly advancing technology.
The process of laser cutting involves the use of a concentrated beam of light, typically generated by a carbon dioxide (CO2) or fibre laser. This beam is directed onto the surface of the material, where it delivers a high amount of energy in a small focal spot. The intense heat of the laser beam rapidly melts, vaporizes, or burns away the material, leaving behind a precise cut or incision. The precise control over the laser beam’s power, speed, and focus allows for exceptional accuracy and the ability to cut intricate shapes and patterns.
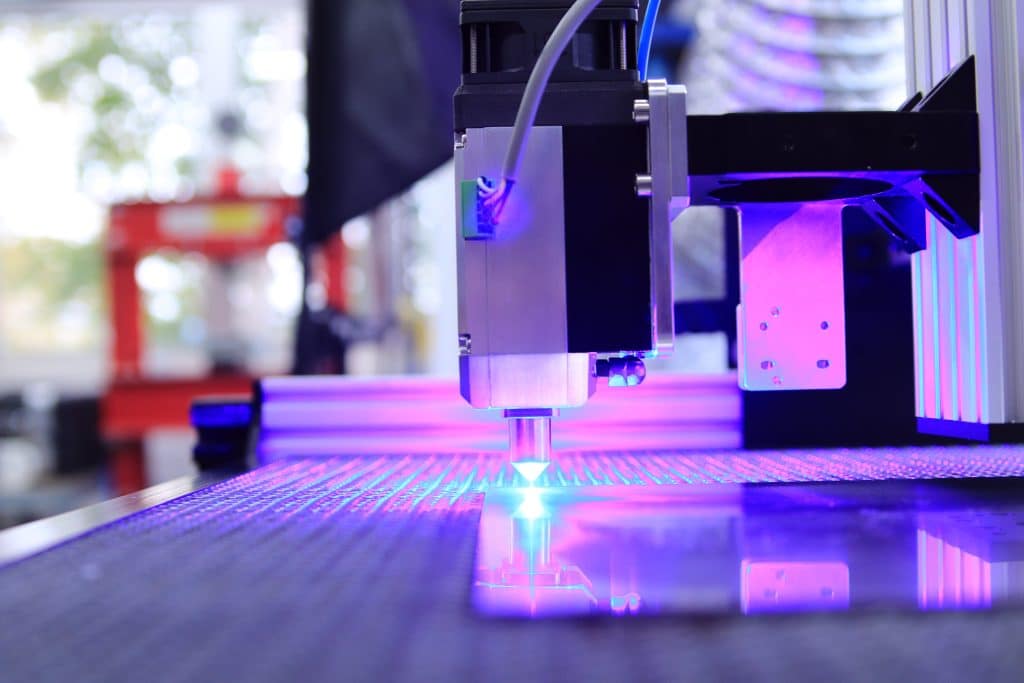
How Laser Cutting Works
Laser cutting operates by utilizing a highly intense light beam, known as the laser beam, which consists of a single wavelength or colour. In the case of a typical CO2 laser, the wavelength falls within the Infra-Red spectrum, rendering it invisible to the human eye. As the laser beam travels from the laser resonator, responsible for generating the beam, it passes through the machine’s beam path. This path may involve multiple mirrors or “beam benders” that redirect the beam until it reaches its final destination on the plate. Just before reaching the plate, the focused laser beam passes through the bore of a nozzle, which also accommodates the flow of a compressed gas, such as Oxygen or Nitrogen.
This focusing process takes place to ensure the shape of the focus spot and the energy density within that spot are consistently round, centred, and at the desired intensity. By converging the large laser beam into a small focal point, the heat density at that spot becomes extremely high. To illustrate this, consider the effect of using a magnifying glass to concentrate the sun’s rays on a leaf, which can ignite a fire. Now envision focusing 6 kilowatts of energy into a single spot, giving an idea of the intense heat generated.
The high power density of the laser beam leads to rapid heating, melting, and, in some cases, vaporization of the material being cut. For instance, when cutting mild steel, the laser beam’s heat initiates an oxy-fuel burning process, with pure oxygen employed as the laser cutting gas, similar to an oxy-fuel torch. On the other hand, when cutting stainless steel or aluminium, the laser beam simply melts the material, and high-pressure nitrogen is used to blow the molten metal out of the kerf.
In a CNC laser cutter, the laser cutting head moves over the metal plate following the shape of the desired part, effectively cutting it out. A capacitive height control system ensures an accurate distance is maintained between the end of the nozzle and the plate being cut. This distance is crucial as it determines the focal point’s location relative to the plate’s surface. Adjusting the focal point’s position, whether above, at, or below the surface, can influence the quality of the cut.
How Precise is Laser Cutting?
• Accuracy and Tolerance Levels
Precision is paramount in many manufacturing processes to ensure components fit together seamlessly and meet industry standards. Laser cutting excels in achieving high levels of accuracy, often within a few thousandths of an inch. This precision enables the production of parts with tight tolerances, ensuring precise fits during assembly. For example, in the aerospace industry, laser cutting is utilized to manufacture intricate turbine blades with precise dimensions, ensuring optimal engine performance.
• Edge Quality and Smoothness
Clean, burr-free edges are essential in many fabrication processes for structural integrity and visual appeal. Laser cutting delivers superior edge quality and smoothness. The laser beam precisely melts or vaporizes the material along the cutting path, resulting in sharp and smooth edges without the need for secondary finishing operations. This advantage is particularly beneficial in applications such as architectural metalwork or stainless steel fabrication, where a pristine edge finish is essential for corrosion resistance and aesthetics.
• Minimal Material Distortion
Minimizing material distortion is crucial in fabrication processes to maintain structural integrity and dimensional accuracy. Laser cutting, as a non-contact process, reduces the risk of material distortion, warping, or damage. This advantage is particularly important when working with delicate or heat-sensitive materials. The precise and localized heating of the laser beam minimizes the heat-affected zone, preserving material properties and avoiding deformations.
Factors Affecting Precision in Laser Cutting
Achieving optimal precision in laser cutting involves considering several factors that influence the cutting quality and efficiency. Understanding and controlling these factors are crucial for obtaining accurate and high-quality cuts.
• Laser Power and Beam Quality
The laser output power plays a significant role in determining the cutting quality. When cutting thicker materials, higher laser power is often required to achieve satisfactory results. However, the beam mode, which refers to the distribution of energy in the laser beam’s cross-section, becomes particularly important at lower power levels. The focus spot obtains higher power density, resulting in better cutting quality. The modes of the laser beam may vary during the machine’s operation due to factors such as optical element conditions, changes in laser working gas mixture, and flow fluctuations. By selecting the appropriate laser power and ensuring the beam mode remains consistent, precise and reliable cutting can be achieved.
• Focus and Spot Size
The positioning of the focus relative to the workpiece surface significantly affects the cutting quality. In most cases, the focus is set just above or slightly below the workpiece surface to achieve optimal results. Maintaining a constant and accurate relative position between the focus and the workpiece is crucial for stable cutting quality. Adjusting the focus to the ideal position results in smaller slits, higher efficiency, and improved cutting speed. The spot size, which is directly proportional to the focal length of the lens, also impacts the cutting effect. Short focal length lenses produce small spot sizes, providing high power density at the focus and making them suitable for high-speed cutting of thin materials. Long focal length lenses, on the other hand, offer a wider focal depth and sufficient power density, making them more suitable for cutting thick workpieces.
• Material Thickness and Type
Different materials require adjustments in laser cutting parameters to achieve desired results. The spot size of the laser beam plays a crucial role in the cutting effect, and it is influenced not only by the laser beam quality but also by the material itself. For instance, materials with high reflectivity like copper pose challenges for spot formation, necessitating higher requirements for copper laser cutting machines compared to ordinary metals. Additionally, material thickness affects the cutting outcome. Increasing the thickness of the material leads to relatively more burrs and uneven cross-sections. To maintain consistent cut quality, laser power needs to be increased accordingly.
• Cutting Speed and Assist Gas
Cutting speed is directly linked to the laser power density, and increasing the power density enhances cutting speed. However, cutting speed is also influenced by the material’s density, thickness, and other factors. Increasing power, improving beam mode, reducing spot size, and cutting low-density or thin materials can enhance cutting speed within certain ranges. The choice of assist gas and its pressure also affects cutting quality. Coaxially ejected with the laser beam, the assist gas serves multiple purposes, including lens protection, slag removal, and material treatment. Different materials require different assist gases, such as compressed air, inert gases, or active gases like oxygen for metal cutting. Adjusting the gas pressure appropriately based on material thickness and cutting speed helps maintain optimal cutting performance.

Future Trends in Laser Cutting Technology
Increased use of high-power output fibre lasers
Increased use of high-power output fibre lasers:
The laser machinery industry is experiencing an increased use of high-power output fibre lasers. These lasers enhance the efficiency of laser machines by enabling faster and more accurate cutting and processing of materials. High-power output fibre lasers are capable of cutting through thick and dense materials with ease, making them ideal for a wide range of applications. Some examples of laser machinery that utilize high-power output fibre lasers include:
Industrial laser cutters: These machines employ high-power output fibre lasers to cut materials such as metal, plastic, and wood with precision and speed.
Laser welding machines: These machines utilize high-power output fibre lasers to weld metal components together, creating strong and seamless bonds.
Laser marking machines: These machines use high-power output fibre lasers to mark or engrave materials like metal, plastic, and wood with exceptional precision and clarity.
Laser cleaning machines: These machines utilize high-power output fibre lasers to remove thick coatings, rust, and other contaminants from various materials.
Laser cladding machines: Also known as laser cladding systems, these machines apply a thin layer of material onto a substrate to enhance its surface properties, such as wear resistance, corrosion resistance, and thermal conductivity.
Adoption of smart manufacturing technologies
Smart manufacturing technologies, including automation, data analytics, and the Internet of Things (IoT), are being increasingly adopted in the laser machinery industry. These technologies help maximize efficiency by enabling effective monitoring and control of production processes. While smart manufacturing technologies are commonly adopted by large companies with complex production processes, retailers and wholesalers may also utilize them to improve supply chain management and reduce costs. Some examples of smart manufacturing laser machinery include:
Automated laser cutting machines: These machines employ lasers to cut materials like metal and plastic with precision and can be programmed to operate automatically based on predetermined instructions.
Smart welding robots: These robots use lasers to weld materials together with precision and can be programmed to operate automatically based on predetermined instructions.
IoT-enabled laser marking machines: These machines use lasers to mark materials such as metal and plastic with text, graphics, or other identifying information. They can be connected to the internet for remote monitoring and control.
Development of hybrid laser cutting systems
Hybrid laser cutting systems are being developed to enhance efficiency in the laser machinery industry. These systems combine different laser technologies within a single machine, allowing for versatile cutting capabilities and increased precision and speed. Hybrid laser cutting systems often incorporate features like intelligent process control, automatic nozzle changing, and automatic material handling to further improve efficiency and productivity. Examples of this machines used in various applications include:
Hybrid fibre lasers: These hybrid lasers combine a fibre laser with a CO2 laser, enabling cutting of a wide range of materials, including metals, plastics, and wood.
Hybrid laser scanning systems: These systems combine laser scanning technology with a CO2 laser, facilitating cutting of intricate shapes and patterns with high precision and speed.
Hybrid laser micro-machining systems: These systems combine a laser with a micro-machining tool, allowing for precise cutting and drilling of small and delicate parts.
Increased use of 3D laser cutting
The increased use of 3D laser cutting allows manufacturers to produce complex and intricate parts and shapes with greater precision and speed. 3D laser cutters are employed to cut and shape materials such as metal, plastic, and wood based on digital designs. Examples of 3D laser cutting machinery include CO2 laser cutters, fibre laser cutters, and plasma cutters.
Conclusion
Laser cutting technology has revolutionized various industries by providing precise, efficient, and versatile cutting and processing solutions. The introduction highlighted the fundamental principles and applications of laser cutting, emphasizing its wide range of uses across materials like metal, plastic, wood, and more. The subsequent paragraphs explored the future trends in laser cutting technology, including the increased use of high-power output fibre lasers, adoption of smart manufacturing technologies, development of hybrid laser cutting systems, utilization of artificial intelligence and machine learning, growing popularity of 3D laser cutting, and expanding applications of laser cutters in various industries. These trends are driving advancements in the field, enhancing efficiency, precision, and productivity. As laser cutting technology continues to evolve, it holds great potential for further advancements and innovative applications in the future.