Every heavy vehicle is a testament to the remarkable manufacturing processes behind its essential parts. From the robust components that endure colossal loads to the intricate systems that ensure peak performance, the creation of heavy vehicle parts is a fascinating blend of craftsmanship, innovation, and precision. Within this article, we venture into the fascinating realm of manufacturing heavy vehicle parts, exploring the materials and processes that drive this vibrant industry.
Heavy vehicles need to endure tremendous loads and extreme conditions and therefore require robust parts that can stand the test of time. Take, for instance, the gearboxes that enable these vehicles to conquer challenging terrains. The gears, shafts, and bearings within these assemblies must be meticulously crafted and flawlessly assembled to withstand the immense forces and torques they encounter. Any compromise in their manufacturing quality or material selection could jeopardize not only the vehicle’s performance but also the safety of those who depend on them.
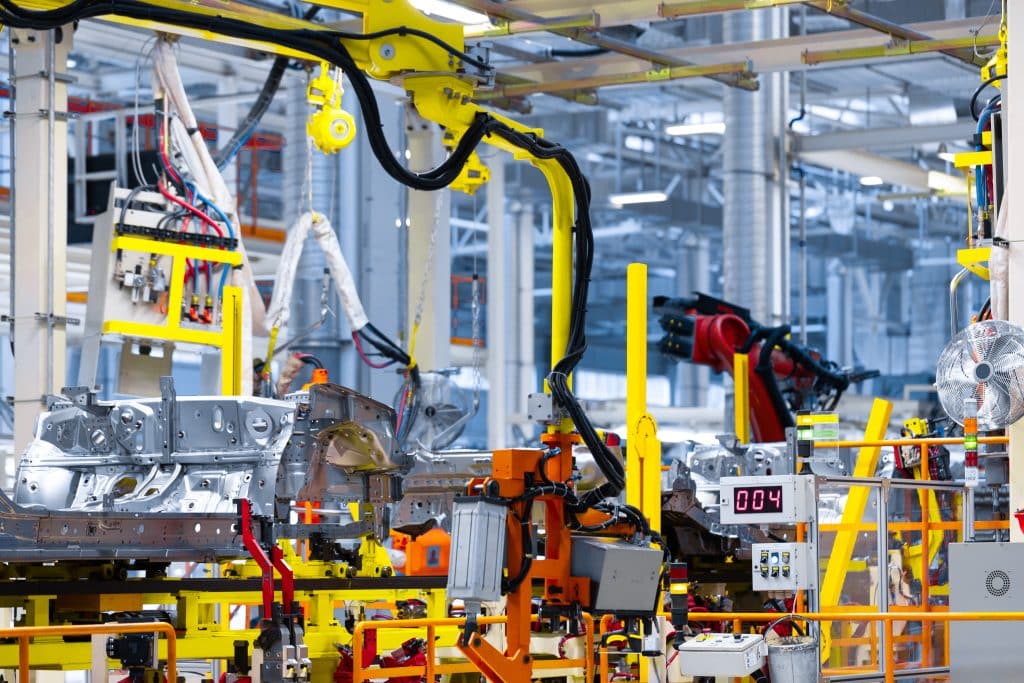
Materials Used in Manufacturing Heavy Vehicle Parts
Exploring the Key Materials
The selection of materials plays a pivotal role in the manufacturing of heavy vehicle parts, as it directly influences the strength, durability, and performance of these components. Let’s take a closer look at some of the key materials commonly used:
- Steel Alloys: Steel is essential to heavy vehicle parts manufacturing due to its exceptional strength and versatility. High-strength steel alloys, such as advanced high-strength steel (AHSS), provide excellent structural integrity while reducing weight. For example, AHSS is used in critical components like frames, suspension systems, and axles, enabling heavy vehicles to withstand heavy loads without compromising safety and fuel efficiency.
- Aluminium: Aluminium and its alloys are prized for their lightweight properties, making them ideal for applications where weight reduction is crucial without sacrificing strength. Heavy vehicle parts like engine blocks, wheels, and body panels benefit from aluminium’s high strength-to-weight ratio. Additionally, aluminium offers better corrosion resistance compared to steel, prolonging the lifespan of these parts.
Cast Iron: Cast iron finds its place in heavy vehicle parts that require exceptional durability and heat resistance, such as engine blocks and cylinder heads. Its high tensile strength, resistance to thermal expansion, and excellent damping properties make it an indispensable material in demanding environments. However, due to the drive for greater fuel efficiency, cast iron is increasingly being replaced by lighter, albeit more expensive, materials such as aluminium.
Factors Influencing Material Selection
The choice of materials in heavy vehicle parts manufacturing is influenced by several key factors, including:
- Strength and Durability Requirements: Heavy vehicles operate under extreme conditions and endure heavy loads, necessitating materials with exceptional strength and durability to withstand these demanding environments.
- Weight Reduction Goals: Reducing the weight of heavy vehicle parts enhances fuel efficiency and overall performance. Therefore, materials with high strength-to-weight ratios, such as advanced alloys and composites, are preferred.
- Cost Considerations: Balancing material costs with desired performance characteristics is crucial. Manufacturers often seek cost-effective materials that meet the required specifications without compromising on quality.
- Manufacturing Processes: Different materials may require specific manufacturing techniques, influencing material choices to ensure efficient production and assembly.
By carefully considering these factors, manufacturers can select the most suitable materials for heavy vehicle parts, striking a balance between strength, durability, weight reduction, and cost-effectiveness.

Casting: Shaping the Foundation
Understanding the Casting Process
Casting serves as a cornerstone in heavy vehicle parts manufacturing, employing the method of pouring molten metal into moulds to create components of various shapes and sizes. This versatile process offers significant benefits, including:
- Design Flexibility: Casting allows manufacturers to produce intricate and complex shapes, offering design flexibility that may be challenging or costly to achieve through other manufacturing techniques.
- Material Adaptability: Casting accommodates a wide range of metals and alloys, including iron, steel, aluminium, and their respective alloys. This versatility provides manufacturers with the freedom to select materials that meet specific performance requirements.
- Cost-Effectiveness: Casting is often an economical choice, particularly for large-scale production, as it minimizes material waste and reduces the need for extensive machining.
Different Casting Methods and Their Applications
- Sand Casting: Among the widely used casting methods in heavy vehicle parts manufacturing, sand casting involves creating moulds using a mixture of sand and binder material. It proves especially suitable for the production of large and complex parts like engine blocks and transmission housings. Similarly to Investment casting, this process is usually more suitable for smaller production volumes.
- Investment Casting: Also referred to as “lost-wax casting,” investment casting entails the creation of a wax pattern of the desired part, coating it with a ceramic shell, and then eliminating the wax through melting. This technique enables the production of intricate and highly detailed components, such as turbine blades, with superior surface finish.
- Die Casting: Making use of reusable moulds known as dies, die casting enables the production of high-volume parts with precise dimensions and tight tolerances. This method finds application in manufacturing aluminium and magnesium alloy components, including wheels and engine brackets. Since the tooling required for this process can be a huge investment, this process is most suitable for large production volumes, where a low unit price is essential.
Casting processes find extensive application in the automotive industry, enabling the manufacture of vital heavy vehicle components like engine blocks, cylinder heads, and transmission cases. The strength, versatility, and cost-effectiveness of casting render it an indispensable process for meeting the demanding requirements of modern manufacturing.
Forging: Transforming Strength
Forging in Manufacturing Heavy Vehicle Parts
Forging is heavily adopted in heavy vehicle parts manufacturing. This process involves shaping metal through the application of localized compressive forces, imparting superior strength and durability to the components, and making it a preferred method in the industry. Key aspects of forging include:
- Metallurgical Integrity: Forging eliminates defects like porosity, gas pockets, and shrinkage, resulting in parts with enhanced structural integrity and mechanical properties.
- Grain Flow: During forging, the metal’s grain structure is realigned and elongated, enhancing its strength and resistance to fatigue, making it particularly suitable for heavy-duty applications.
- Consistency: By utilizing precise tooling and controlled processes, forging ensures high repeatability and consistency in producing parts, meeting stringent quality requirements.
Types of Forging Techniques for in Manufacturing Heavy Vehicle Parts
- Open-Die Forging: Also known as smith forging or hand forging, open-die forging involves the shaping of metal between flat or simple-shaped dies. This method is commonly used for manufacturing large, custom-designed components like shafts, axles, and crankshafts for heavy vehicles.
- Closed-Die Forging: Closed-die forging, or impression-die forging, employs shaped dies that contain impressions of the desired part’s final shape. The metal is compressed between these dies to form the component. This technique is suitable for producing intricate parts with high dimensional accuracy, such as gears, connecting rods, and suspension components.
- Roll Forging: Roll forging utilizes cylindrical or flat dies to gradually shape the metal, allowing for continuous and efficient production of parts like long shafts or bars with reduced material waste.
Machining: Precision at Its Core
CNC Machining in manufacturing heavy vehicle parts
Machining is a fundamental process in heavy vehicle parts manufacturing, enabling precise shaping and refinement of components to meet stringent specifications. This subtractive manufacturing technique involves removing material from the workpiece to achieve the desired form, dimensions, and surface quality. Key aspects of machining include:
- Precision and Accuracy: Machining processes excel in delivering exceptional precision and tight tolerances, ensuring the production of components with exacting dimensions and superior surface finish.
- Adaptability and Versatility: Machining techniques can be applied to a wide range of materials, including metals, alloys, and composites, providing manufacturers with the flexibility to create components for diverse heavy vehicle applications.
Efficiency and Automation: Advanced machining technologies, combined with automation, empower manufacturers to achieve efficient production rates, optimizing productivity and ensuring timely delivery of high-quality parts.
Techniques Driving Manufacturing Heavy Vehicle Parts
- Turning: This machining operation involves rotating the workpiece while a cutting tool removes material, resulting in cylindrical components. Turning is extensively used in the production of heavy vehicle parts such as shafts, axles, and bearings.
- Milling: By employing rotary cutters, milling removes material from the workpiece to create complex shapes and features. It is a versatile technique employed in manufacturing components like engine blocks, transmission cases, and chassis parts.
- Drilling: Drilling uses a rotating cutting tool to create holes in the workpiece. It plays a critical role in heavy vehicle parts manufacturing, facilitating the installation of fasteners, fluid passages, and other vital features.
Crafting High-Quality Components through Machining
Machining processes contribute significantly to the production of high-quality heavy vehicle parts:
- Surface Finishing: Machining operations, including grinding, polishing, and honing, enable the attainment of precise surface finishes, enhancing both aesthetics and performance.
- Dimensional Precision: Machining techniques allow for the production of parts with tight tolerances, ensuring accurate fit and assembly within heavy vehicle applications.
- Customization and Flexibility: Machining provides the capability to create customized components tailored to specific requirements, meeting the unique needs of heavy vehicle manufacturers.
Welding: Bonding Strength
Exploring Welding
Welding plays a crucial role in the manufacturing of heavy vehicle parts, providing a reliable and robust method for joining metal components. It involves the fusion of materials through the application of heat, resulting in a strong bond that can withstand the demanding operating conditions of heavy vehicles. Key aspects of welding include:
- Joining Capabilities: Welding techniques enable the connection of various metal parts, allowing for the creation of complex assemblies and structures in heavy vehicles.
- Strength and Durability: Welded joints exhibit excellent strength, durability, and resistance to fatigue, ensuring the structural integrity and longevity of heavy vehicle components.
- Versatility: Welding methods can be applied to a wide range of metals, including steel, aluminium, and their alloys, offering versatility in heavy vehicle manufacturing.
Versatile Welding Methods for Manufacturing Heavy Vehicle Parts
Arc Welding: This widely used welding method utilizes an electric arc to generate intense heat, melting the base metals and forming a strong bond upon cooling. Within arc welding, different techniques include:
- Shielded Metal Arc Welding (SMAW): Also known as stick welding, SMAW employs a consumable electrode covered in flux, providing protection against atmospheric contamination during the welding process. It is commonly used in heavy vehicle manufacturing for applications such as frame fabrication and structural repairs.
- Gas Metal Arc Welding (GMAW): GMAW, also referred to as MIG (Metal Inert Gas) welding, employs a continuously fed wire electrode and a shielding gas to protect the weld pool. This method is frequently utilized in the production of heavy vehicle components, including body panels, fuel tanks, and exhaust systems.
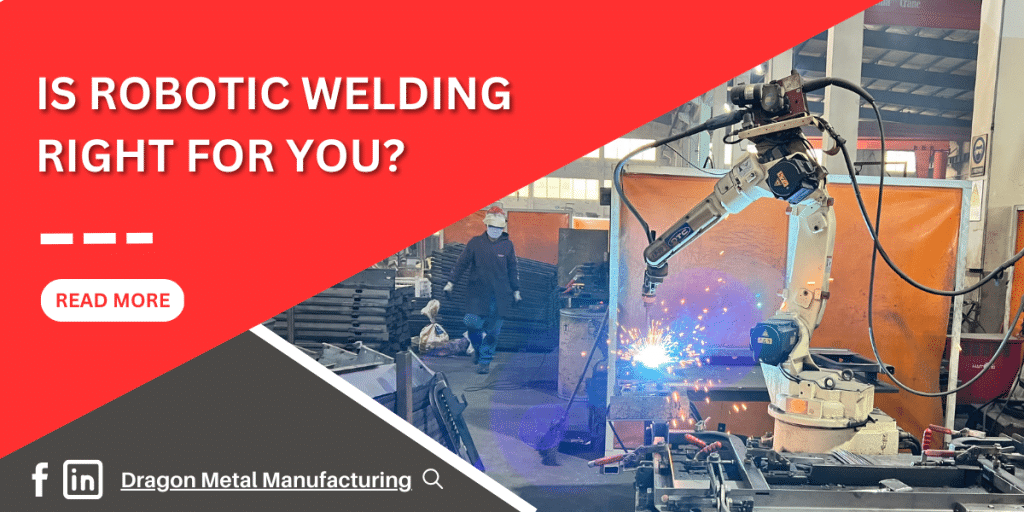
Resistance Welding: This group of welding techniques involves the application of pressure and electrical current to create a bond between metal parts. Examples of resistance welding methods include:
- Spot Welding: Spot welding involves the localized application of heat and pressure to join overlapping metal sheets, commonly used in heavy vehicle manufacturing for applications such as body panels, brackets, and reinforcements.
- Seam Welding: Seam welding is employed to create continuous, leak-proof welds along the length of overlapping metal sheets, ensuring the integrity of welded joints in heavy vehicle fuel tanks, exhaust systems, and chassis components.
Versatile Welding Methods for Manufacturing Heavy Vehicle Parts
- Friction Stir Welding (FSW): FSW is a solid-state welding technique that utilizes frictional heat generated by a rotating tool to join metal components without melting the base materials. It is increasingly employed in the production of heavy vehicle parts such as aluminium body panels, reducing weight while maintaining structural integrity.
- Laser Beam Welding (LBW): LBW employs a focused laser beam to generate heat, melting and bonding metal components with precision. This welding method finds application in the manufacturing of heavy vehicle engine components, transmission assemblies, and precision sheet metal parts.
Top 6 Trends and Innovations in Manufacturing Heavy Vehicle Parts
The heavy vehicle parts manufacturing industry is experiencing a remarkable transformation driven by cutting-edge technologies and innovative approaches. These advancements are reshaping the landscape, enhancing productivity, sustainability, and overall operational efficiency. Let’s explore the top trends and innovations propelling the industry forward:
Artificial Intelligence (AI)
- AI-driven Predictive Maintenance: AI-powered systems can analyse real-time data from heavy vehicles and predict maintenance needs, enabling proactive servicing and reducing downtime.
- Autonomous Vehicles: AI technology plays a pivotal role in the development of autonomous heavy vehicles. Leading manufacturers like Tesla and Volvo are investing in self-driving technologies, envisioning a future where heavy vehicles can operate without human intervention, improving safety and efficiency.
Advanced Robotics
- Robotic Automation: Heavy vehicle parts manufacturing benefits from robotic automation, where robots handle repetitive tasks with precision and speed. Robotic arms can perform complex welding operations, reducing human error and increasing production efficiency. Companies like Fanuc and ABB provide advanced robotic solutions for heavy manufacturing applications.
- Collaborative Robots (Cobots): Cobots work alongside human operators, enhancing safety and productivity on the factory floor. In heavy vehicle manufacturing, cobots assist with heavy lifting, assembly, and intricate tasks. Universal Robots offers cobot solutions that improve ergonomics and streamline production processes.
Industrial Internet of Things (IIoT)
- Connected Machinery: IIoT enables the integration of sensors and smart devices, allowing real-time monitoring and data collection from heavy vehicle manufacturing equipment. This data helps optimize production, improve equipment performance, and enable predictive maintenance.
- Supply Chain Optimization: IIoT facilitates end-to-end visibility and traceability in the supply chain, streamlining inventory management, and optimizing logistics. Heavy vehicle manufacturers can monitor the movement of components, reduce lead times, and enhance overall supply chain efficiency.
Sustainability
- Energy-efficient Manufacturing: Heavy vehicle parts manufacturing is adopting energy-efficient technologies to minimize environmental impact. Companies like Scania and Volvo, for example, are investing in sustainable manufacturing processes, reducing emissions, and optimizing energy consumption throughout the production cycle.
- Lightweight Materials: The use of advanced lightweight materials, such as aluminium alloys and composites, reduces the weight of heavy vehicle components, leading to improved fuel efficiency.
Immersive Technology
- Virtual Reality (VR) and Augmented Reality (AR): Heavy vehicle manufacturers utilize VR and AR for design reviews, training simulations, and assembly guidance. These technologies enhance collaboration, reduce errors, and improve workforce efficiency. Companies like PACCAR and Caterpillar leverage VR and AR to optimize design processes and training programs.
These trends and innovations signify the evolving nature of heavy vehicle parts manufacturing. By embracing AI, advanced robotics, IIoT, sustainability practices and immersive technology, companies can unlock new opportunities, drive operational excellence, and remain at the forefront of the industry’s transformation.
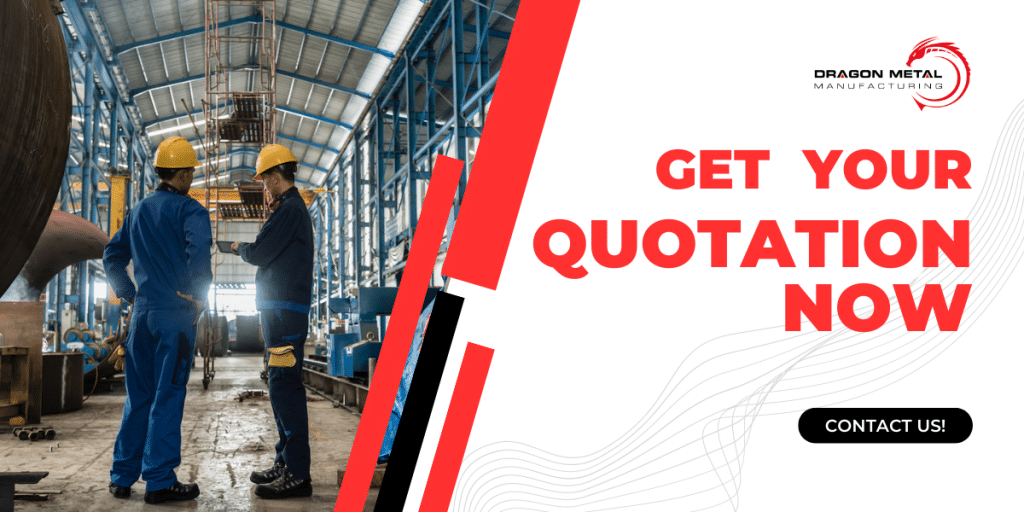
Conclusion
The manufacturing of heavy vehicle parts is both complex and dynamic and requires a combination of advanced materials and sophisticated techniques. From the foundational methods of casting and forging to the precision of machining and the strength of welding, each step plays a crucial role in creating durable and reliable heavy vehicle parts. The industry is constantly evolving, with trends such as artificial intelligence, advanced robotics, and sustainable manufacturing driving innovation.