Carbon fibre is a stranded material that consists of tens of thousands of singular graphite fibres. This material, alongside its composites, has been dubbed the ‘wonder material of the century’ due to its quite interesting characteristics. Carbon fibre is approximately 4 times stronger than aluminium, 75 % lighter than steel, and 1.7 times the stiffness of aluminium.
Other important selling points of carbon fibre include its ease of fabrication, the aesthetics it brings to the table, and the excellent stiffness to weight ratio it offers. These features are the major reasons why engineers, manufacturers, and industrial designers utilise carbon fibres across the automotive, aerospace, healthcare, heavy equipment, and consumer goods industries. This article will discuss the pros and cons of carbon fibre and provide examples of its applications.
Understanding the Pros of Using Carbon Fibre
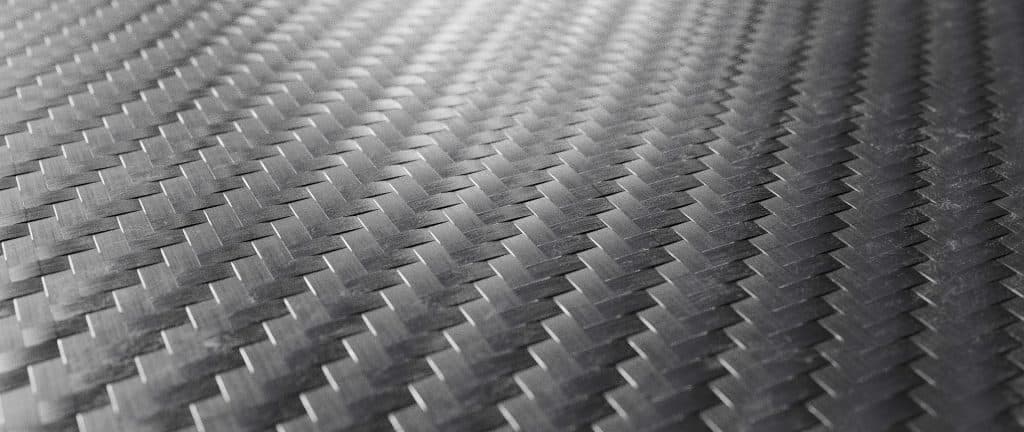
When talking about utilising carbon fibre in metal fabrication or fabrication in general, it is important to note that diverse carbon fibre composites are used. These composites variously consist of plastic polymers, glass, asbestos, or wood depending on a project’s requirement. Despite this diversity of options, carbon fibre reinforcement polymer (CFRP) is the most common option used by fabricators. The pros of using carbon fibre in fabrication include:
- High Tensile Strength to Weight Ratio – The automotive and aerospace industry relies on lightweight materials with extensive tensile strength and aesthetics to produce body parts and interior components that ensure safety. Although steel meets the strength requirement, it is too heavy. Aluminium may be light but not lighter or more aesthetically pleasing compared to carbon fibre. Hence, the industrial sector relies on carbon fibre to produce lightweight parts with extensive tensile strength.
- Extensive Durability – Consumers prefer quality products with extended life cycles that are also aesthetically designed. Carbon fibre provides the industrial sector with a very durable material to produce components that can stand the test of time. The material is resistant to corrosion-causing agents and vibrations. Carbon fibre also functions optimally within environments that produce moisture and can withstand the wear and tear that occurs from regular use.
Resistance to Radiation and X-ray Translucency – The healthcare industry uses medical devices that rely on carbon fibre for a diverse set of reasons. These reasons include its transparency when x-rayed and its resistance to radiation. Hence, carbon fibre is viewed as a viable material to replace metal alloys when developing devices and implants for patients. It is also important to note that carbon fibre does not usually cause irritations or other adverse reactions when in contact with the human skin.
Cons of Using Carbon Fibre for Fabrication
The process associated with developing carbon fibre and its composite materials consists of two processes – a chemical and mechanical process. The mechanical process involves drawing long fibres and heating them to implement a carbonisation process that drives out oxygen. The chemical process involves heating the fibre within specific chemical atmospheres to cause chemical reactions that reinforce the fibre, giving it the durability it is known for.
Together, these processes are expensive. Thus, the first con associated with carbon fibre is the cost of purchasing its composites. Other disadvantages include:
- Thermal Conductivity – Carbon fibre is extremely conductive and requires strict insulation when used in specific industrial scenarios. For example, for the production of domestic utility products, carbon fibre isn’t used due to its thermal conductivity.
- High Repair Costs – Although a durable material, time and regular use mean carbon fibre components will eventually begin to show signs of wear, and eventually a repair may be necessary. Carbon fibre is difficult to repair compared to the maintenance associated with metal fabricated parts. The repair cost and material cost are its major disadvantages because its thermal conductivity can be worked around.
Applications of Carbon Fibre
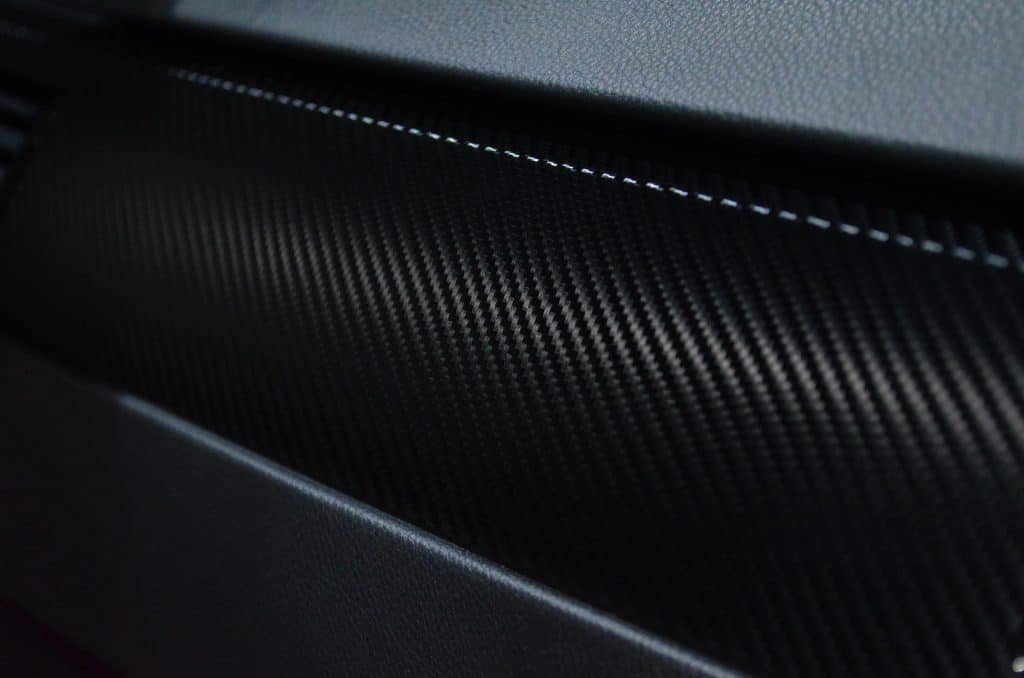
Carbon fibre is a popular fabrication material used across the industrial sector to produce durable lightweight parts. The table below provides some of the popular use cases for carbon fibre:
Carbon Fibre | Automotive Industry | Aerospace Industry | Healthcare Industry | Consumer Goods/ Utility/Sports Industries |
Uses | Chassis or body parts, wheels, rims, interior finishing, and cabinet design. | Fuselage, body components, wings, tails, and interior finishing. | Imaging machine beds and support structures, power tools, prostheses, and implants. | Bicycles, athletic shoes, wallets, mobile devices, and fashion items. |
Use Cases | For lightweight durable parts to support the vehicle’s structure. | For its lightweight durability and aesthetics. | For their skin-friendly nature and durability. | For their pleasing aesthetics, durability, and skin-friendly characteristics. |
Learn more about the pros and cons of carbon fibre in fabrication and how you can use it for your projects by speaking to the experts today. Contact a Dragon Metal Representative.