Sheet metal fabrication is the process of transforming flat sheets of metal into different shapes and sizes using various tools and techniques. Sheet metal fabrication is widely used in many industries, but especially in the electronic industry, where precision, durability, and customization is essential. In this blog post, we will explore how sheet metal fabrication meets the needs of the electronic industry, what are the key processes involved, what are the common sheet metals used, and what are some of the applications in this field.
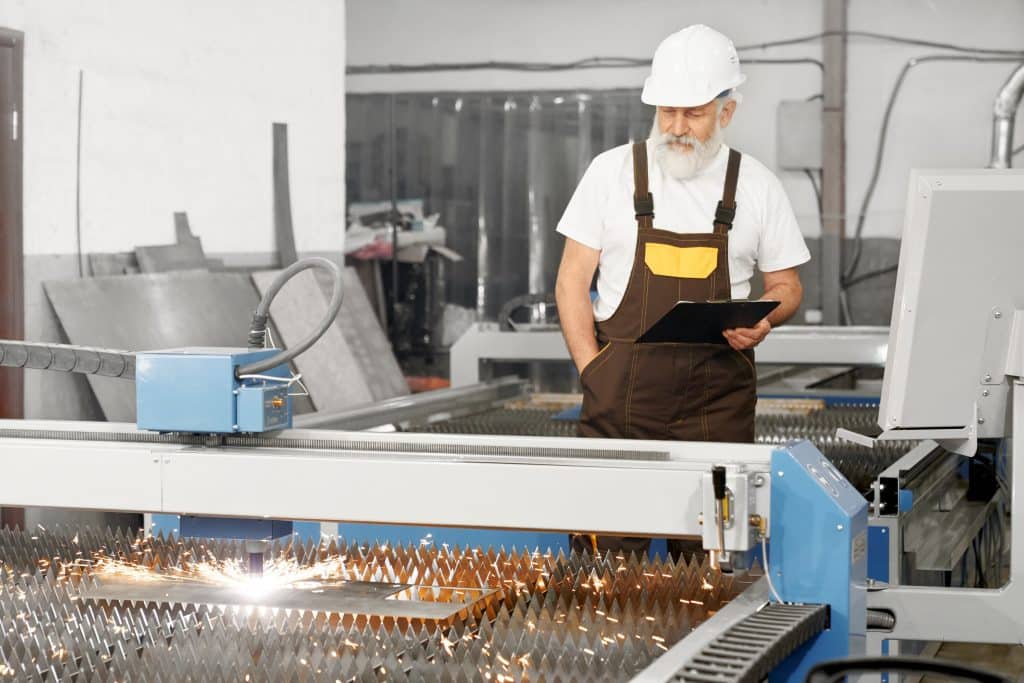
The Electronic Industry’s Need for Precision Metal Fabrication
The electronic industry is constantly evolving and innovating, producing smaller, faster, and smarter products that require high-quality and reliable components. Sheet metal fabrication can provide the following benefits for the electronic industry:
• Miniaturization of Electronic Products: Sheet metal fabrication can produce thin and lightweight parts that can fit into compact spaces and reduce the overall size and weight of electronic products. For example, sheet metal fabrication can create enclosures for printed circuit boards (PCBs), hard drives, and other electronic devices.
• Importance of Durability and Accuracy: Sheet metal fabrication can produce parts that are resistant to corrosion, wear, and tear, and can withstand harsh environments and temperatures. Sheet metal fabrication can also produce parts that have precise dimensions and tolerances, ensuring that they fit and function properly in electronic products.
• Customization: Sheet metal fabrication can produce parts that are tailored to the specific needs and specifications of each customer and project. Sheet metal fabrication can offer a variety of design options, such as holes, slots, bends, curves, and cutouts, to create unique and complex shapes.
• Thermal Management: Sheet metal fabrication can produce parts that can help dissipate heat and prevent overheating in electronic products. For example, sheet metal fabrication can create heat sinks, which are devices that transfer heat from a hot component to a cooler medium, such as air or water.
• Enhanced Aesthetics: Sheet metal fabrication can produce parts that have smooth surfaces and attractive finishes, such as painting, powder coating, or anodizing. These finishes can improve the appearance and durability of the parts, as well as provide protection from corrosion, scratches, and stains.
Key Processes in Sheet Metal Fabrication for Electronics
There are four main processes involved in sheet metal fabrication: cutting, forming, joining, and finishing. Each process has its own advantages and disadvantages, depending on the type of sheet metal, the desired shape and size of the part, and the quality and cost requirements.
Cutting
Cutting is the process of removing excess material from a sheet of metal to create a desired shape or size. There are three common methods of cutting sheet metal: laser cutting, plasma cutting, and water jet cutting. Laser cutting uses a focused beam of light to melt or vaporize the metal. Plasma cutting uses a jet of ionized gas to melt or blow away the metal. Water jet cutting uses a high-pressure stream of water mixed with abrasive particles to erode the metal. These methods can produce precise and accurate cuts with minimal waste and distortion.
Forming
Forming is the process of bending or stretching a sheet of metal into a different shape or angle. There are two common methods of forming sheet metal: press brakes and roll forming. Press brakes use a hydraulic or mechanical press to apply force to a sheet of metal between a punch and a die. Roll forming uses a series of rollers to gradually bend a sheet of metal into a desired shape.
Joining
Joining is the process of connecting two or more pieces of sheet metal together to form a single part. There are three common methods of joining sheet metal: welding, riveting, and adhesive bonding. Welding uses heat or pressure to melt or fuse the edges of the sheet metal together. Riveting uses a metal pin or bolt to fasten the sheet metal together through holes. Adhesive bonding uses a glue or epoxy to stick the sheet metal together.
Finishing
Finishing is the process of applying a coating or treatment to the surface of the sheet metal to improve its appearance or performance. There are three common methods of finishing sheet metal: painting, powder coating, and anodizing. Painting uses a liquid paint to cover the sheet metal with a layer of colour. Powder coating uses an electrostatic charge to spray a dry powder onto the sheet metal, which is then cured by heat to form a hard coating. Anodizing uses an electric current to create a thin layer of oxide on the surface of the sheet metal, which enhances its corrosion resistance and durability.

Sheet Metals Commonly Used in Electronics
Sheet metals are classified by their thickness, which is measured in gauges or millimetres. The thinner the sheet metal, the higher the gauge number. The most common sheet metals used in electronics are:
Aluminium is a lightweight, strong, and ductile metal that has good electrical and thermal conductivity. Aluminium is easy to cut, form, and join, and can be anodized to create various colours and finishes. Aluminium is widely used in electronics for enclosures, heat sinks, component shielding, and mounting brackets.
Stainless steel is a corrosion-resistant, durable, and tough metal that has high strength and hardness. Stainless steel is difficult to cut, form, and join, and requires special tools and techniques. Stainless steel is used in electronics for applications that require high resistance to heat, wear, and chemicals, such as thermal solutions, component shielding, and structural components.
Copper and brass are metals that have excellent electrical and thermal conductivity. Copper and brass are easy to cut, form, and join, and can be plated or coated with other metals to improve their appearance or performance. Copper and brass are used in electronics for applications that require high current or voltage, such as PCBs, wires, connectors, and transformers.
Zinc is a low-cost, soft, and malleable metal that has good corrosion resistance. Zinc is easy to cut, form, and join, and can be coated with other metals to improve its appearance or performance. Zinc is used in electronics for applications that require low weight and cost, such as enclosures, component shielding, and structural components.
Common Applications in The Electronics Industry
Sheet metal fabrication can produce a variety of parts and components for the electronics industry. Some of the common applications are:
Enclosures for Electronics
Enclosures are cases or boxes that house electronic devices or components, such as PCBs, hard drives, monitors, keyboards, etc. Enclosures protect the electronics from dust, moisture, shock, vibration, electromagnetic interference (EMI), radio frequency interference (RFI), etc. Enclosures also provide access to ports, buttons, switches, etc. Sheet metal fabrication can create enclosures that are customized to the shape, size, design, and function of the electronic device or component.
Heat Sinks and Thermal Solutions
Heat sinks are devices that transfer heat from a hot component to a cooler medium, such as air or water. Heat sinks help prevent overheating and improve the performance and lifespan of electronic products. Sheet metal fabrication can create heat sinks that are optimized for the heat dissipation rate, airflow direction, surface area, etc. of the electronic component.
Component Shielding and RF Interference Prevention
Component shielding is the process of covering or enclosing an electronic component with a metal sheet or cage to block or reduce EMI or RFI. EMI or RFI can interfere with the operation or signal of electronic products. Sheet metal fabrication can create component shielding that is tailored to the frequency range, attenuation level, grounding method, etc. of the electronic component.
Mounting Brackets And Structural Components Mounting brackets are devices that support or secure electronic products or components to a surface or structure. Structural components are parts that provide strength or stability to electronic products or components. Sheet metal fabrication can create mounting brackets and structural components that are designed for the load capacity, stress distribution, alignment accuracy, etc. of the electronic product or component.
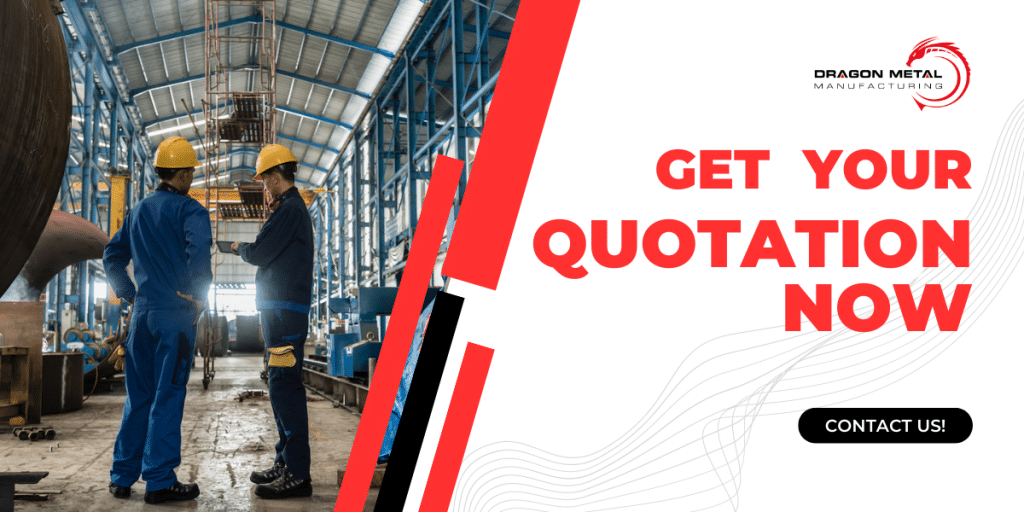
Conclusion
Sheet metal fabrication is a versatile and valuable process for the electronic industry. Sheet metal fabrication can produce parts and components that meet the high standards of precision, durability, and customization required by the electronic industry. Sheet metal fabrication can also offer a range of design options and finishes to enhance the appearance and performance of electronic products. Sheet metal fabrication can create parts and components for various applications in the electronic industry, such as enclosures, heat sinks, component shielding, mounting brackets, and more.