As an engineer, you are likely familiar with the terms Tooling, Fixtures and Jigs but do you fully understand the differences and similarities between these types of equipment used in manufacturing? In this blog post, we will explore the distinct differences and similarities between jigs, tooling, and fixtures, as well as the relationship between tooling and moulds.
Definition of Tooling, Fixtures and Jigs
What are Jigs?
A jig is a type of tool that is used to guide and secure a workpiece in place during the manufacturing process. Jigs are commonly used in drilling, cutting, and grinding operations to ensure that the workpiece is held in a consistent position, which is essential for producing precise and accurate results. Jigs can be simple or complex, depending on the requirements of the manufacturing process.
What are Fixtures?
Fixtures are like jigs in that they hold a workpiece in place during the manufacturing process. However, fixtures are typically more specialized and are designed to hold a specific type of workpiece. For example, a fixture might be used to hold a particular type of part in place during a welding operation. Fixtures are generally more complex than jigs, and they may include a variety of components, such as clamps and guides, to ensure that the workpiece is held in the correct position.

Jigs vs. Fixtures: Key Differences and Similarities
While jigs and fixtures both serve similar purposes, there are key differences and similarities between these two types of equipment.
- Purpose: Jigs are designed to guide and secure a workpiece in place, while fixtures are used to hold a specific type of workpiece in place during a manufacturing process.
- Complexity: Jigs can be simple or complex, depending on the requirements of the manufacturing process. Fixtures are generally more complex than jigs.
- Customization: Both jigs and fixtures are often designed for specific applications and are customized to meet the needs of a particular manufacturing process.
- Cost: The cost of jigs and fixtures can vary greatly, depending on the complexity of the equipment and the materials used. Fixtures are generally more expensive than jigs.
Similarities: Both jigs and fixtures are designed to hold a workpiece in place during a manufacturing process and play a crucial role in ensuring the accuracy and precision of the finished product.
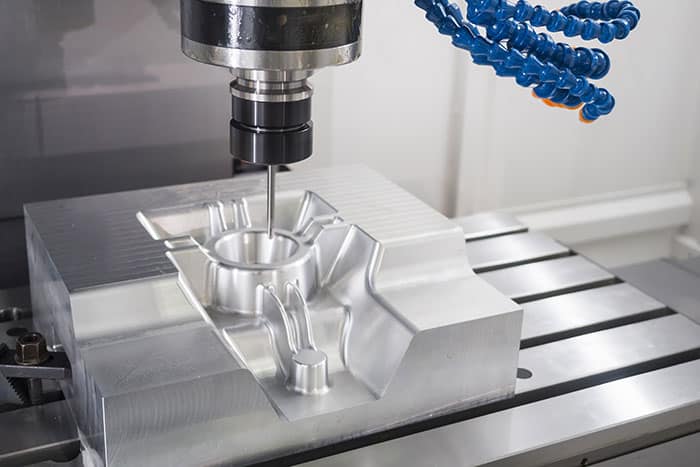
What is Tooling?
Tooling in manufacturing pertains to the creation of moulds, which are composed of a core and cavity, used to produce parts by injecting molten plastic resin. Proper tooling is essential in the production of high-quality and high-quantity parts, which are typically machined from hardened steel. In some cases where lower quantities are required, “soft tooling” is used, and the moulds are machined from aluminium instead of steel. However, this is only suitable for products requiring small batch quantities.
Tooling can be complex in design and construction, with some moulds having inserts, multiple cavities, and conformal cooling to achieve complex geometries, increase the quantity of parts, and improve part quality. However, complex tooling comes at a higher cost and requires longer lead times.
Tooling and Moulds: The Relationship
The relationship between tooling and moulds is significant in the production of plastic parts that are shaped and sized accurately. Moulds and tooling are vital components in the manufacturing process, and their quality and functionality influence the end product’s quality. While different manufacturing processes necessitate various types of moulds, the most prevalent are injection moulding tools and die-casting tools.
2 Common Mould Type
Injection Moulding Tools: Injection moulding tools are used to produce parts made of thermoplastic or thermoset materials. The material is melted and then injected into a mould where it cools and solidifies into the desired shape. Injection moulding tools are typically made of steel or aluminium and are designed to withstand the high pressure and temperature required for the injection moulding process.
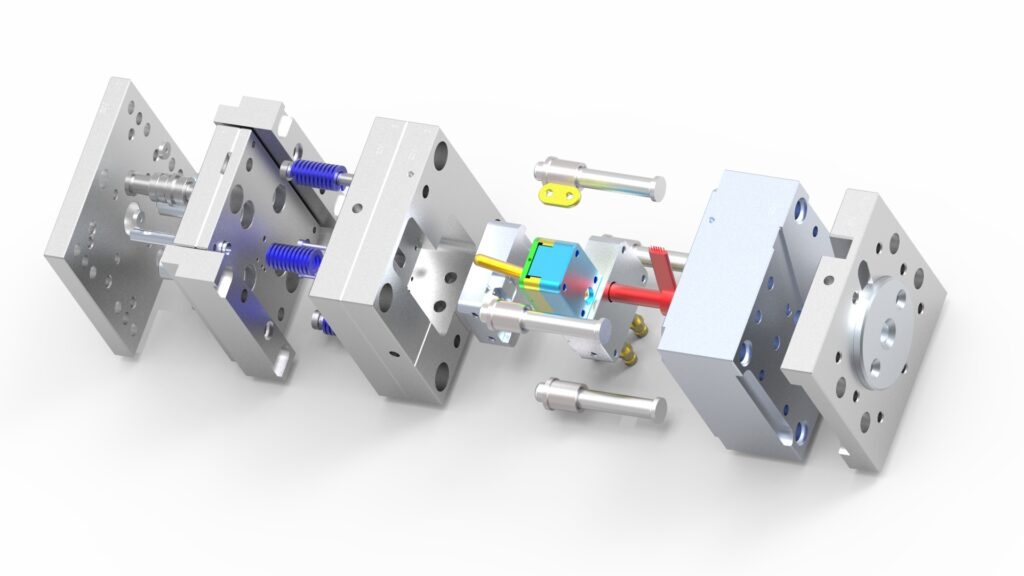
Die-Casting Tools: Die-Casting tools are used in the die-casting process, which involves melting metal alloys and injecting the molten material into a mould under high pressure. The mould is typically made of two halves, and the molten metal is injected into the cavity between the halves. Once the metal has solidified, the mould is opened, and the finished part is ejected. Die-casting tools are typically made of high-strength steel or other metals, and they are designed to withstand the high pressures and temperatures of the die-casting process.
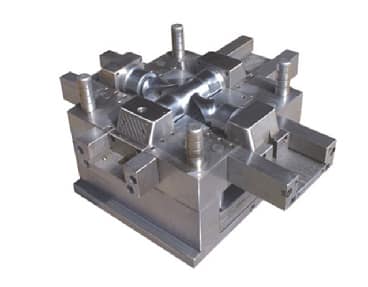
Conclusion
Overall, while tooling, fixtures, and jigs serve different purposes in manufacturing, they share common characteristics and functions. Understanding the differences and similarities between these tools is essential for optimizing production processes, reducing costs, and ensuring high-quality products. The appropriate selection and use of these tools, depend on the specific manufacturing requirements and objectives.