When it comes to injection moulding, achieving the desired quality, functionality, and visual appeal of the final product turning point on surface texture. Surface texture encompasses the tactile and visual characteristics that define a surface, such as its smoothness, roughness, and appearance. It is a result of various factors, including the moulding process, tooling techniques, and material selection. Understanding types of surface textures is paramount in the designing stage based on the functionality of the product being designed.
Surface texture plays an important role in injection moulding for both functional and aesthetic aspects of the final product. Functionally, the surface texture impacts crucial factors such as friction, wear resistance, and part release. It can enhance the performance of moving components by reducing frictional forces, preventing sticking or binding. Additionally, the texture can influence the appearance and perceived quality of the product, making it visually appealing and pleasing to touch. Whether it’s achieving a glossy, matte, or textured finish, the right surface texture selection can significantly enhance the marketability, customer satisfaction, and overall success of injection-moulded products.
Different Types of Mould Surface Textures
Mould surface textures are essential for achieving desired aesthetics and functionality in injection-moulded products. Polishing, classified as category A in injection moulding surface finish standards, results in shiny and glossy parts. The surface is polished using a rotary tool in a non-linear, random fashion, creating a consistent pattern from any viewing angle.
Category B in surface finish standards, sandpaper textures are created using a back-and-forth motion. This technique produces semi-gloss finishes with linear scratches and distinct patterns. Sandpaper finishes are cost-effective and effectively hide mould defects.
Grit stone textures utilize abrasive sanding stones with grit sizes ranging from 320 to 600. These textures create rougher and less flat surfaces compared to sandpaper finishes. The aggressive cutting action of the stones quickly removes mould or tooling marks, leaving a matte finish on plastic parts.
Blasting techniques, corresponding to category D in surface finish standards, involve the use of glass beads or sand to create rougher finishes. The random nature of the blasting results in a non-directional and uniform surface texture. Blasting is commonly used to achieve flat and dull finishes.
EDM, or Electronic Discharge Machining, is a process that produces similar results to spark erosion. The choice of EDM technique depends on the desired features and the material being processed. EDM allows for precise and controlled surface textures.
Satin finishing is a quick process that creates flat surfaces and provides durability. It is particularly effective in covering weld and sink marks on rough surfaces, enhancing the overall appearance and quality of the moulded parts. These techniques provide versatility and options to achieve desired surface textures, enhancing the quality of injection-moulded products.
Types of Surface Textures: SPI Surface Finish Standard
The SPI (Society of the Plastics Industry) surface finish standard is a widely recognized classification system used in the plastic injection moulding industry to define and communicate different surface finishes. It provides a common language for manufacturers, designers, and engineers to specify the desired surface characteristics of injection-moulded products.
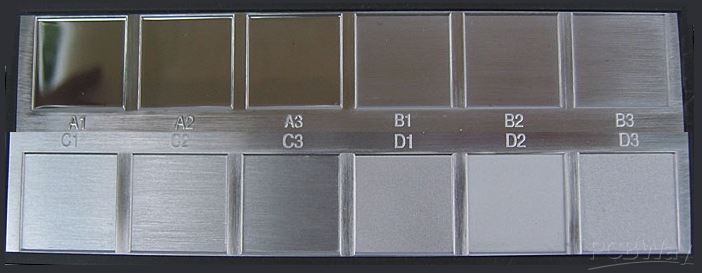
Shiny/Glossy Finish
These grade “A” finishes are characterized by their smooth, glossy appearance and are considered the most expensive options. Achieving these finishes requires hardened tool steel moulds that are buffed using various grades of diamond buff.
The fine-grain buffing paste and random directional rotary polishing method result in a clear texture and light ray scattering, giving a highly glossy finish. These finishes are also known as “Diamond finish,” “buff finish,” or “A finish.”
SPI gloss grades, such as A2, are commonly used in the industry for visually pleasing parts with good release. They are particularly suitable for products requiring a smooth surface finish for both cosmetic and functional reasons.
Grade “A” surface finishes are also employed in the production of optical parts like lenses, mirrors, and visors, where exceptional clarity and gloss are essential.
Semi-Gloss Finish
Semi-gloss finishes are cost-effective options that effectively eliminate machining, moulding, and tooling marks. These finishes are achieved by using different grades of sandpaper applied with linear motion, resulting in a distinctive linear pattern.
SPI semi-gloss surface finishes provide a good visual appearance and help remove mould tool marks. They are often applied to parts that do not serve a decorative or visually significant purpose in the overall product.
Matte Finish
SPI matte finishes are achieved using grit sanding stones, enabling the removal of machining marks while avoiding a glossy appearance. This technique is ideal for product designs that require a subdued or muted look.
With Grade C finishes, the reflection of light is minimized, making fingerprints less conspicuous on frequently handled products. This makes them well-suited for applications like keyboards and laptop frames.
Textured Finish
Textured finishes are widely used in industrial parts and consumer goods, providing a reasonable aesthetic appearance. They are suitable for parts without specific visual requirements.
To create textured finishes, the surface is first smoothed using fine stone powder and then dry blasted using aluminium oxide or glass beads. The random nature of dry blasting results in a smooth and non-directional surface finish.
Textured finishes enhance grip quality, hide deformations and marks, and even help mask fingerprint smudges. They find application in thermoset industrial parts and parts requiring a dull or satin textured finish, such as consumer product handles.
Types of Surface Textures: Mould-Tech Injection moulding surface texture
Mould-Tech specifications are widely used in the industry and are manufactured according to specific Mould-Tech specifications. These surface textures are created through chemical etching or laser-based alteration of the mould cavity. Each Mould-Tech texture is denoted by an MT- followed by a five-digit code and is classified based on the serial number and texture depth.
Mould-Tech A
Serie Number | Texture Depth (Inch) | Texture Depth (Meter) | Draft Angle |
MT-11000 | 0.0004 | 0.01016 | 1 |
MT-11010 | 0.001 | 0.0254 | 1.5 |
MT-11020 | 0.0015 | 0.0381 | 2.5 |
MT-11030 | 0.002 | 0.0508 | 3 |
MT-11040 | 0.003 | 0.0762 | 4.5 |
MT-11050 | 0.0045 | 0.1143 | 6.5 |
MT-11060 | 0.003 | 0.0762 | 4.5 |
MT-11070 | 0.003 | 0.0762 | 4.5 |
MT-11080 | 0.002 | 0.0508 | 3 |
MT-11090 | 0.0035 | 0.0889 | 5.5 |
MT-11100 | 0.006 | 0.1524 | 9 |
MT-11110 | 0.0025 | 0.0635 | 4 |
MT-11120 | 0.002 | 0.0508 | 3 |
MT-11130 | 0.0025 | 0.0635 | 4 |
MT-11140 | 0.0025 | 0.0635 | 4 |
MT-11150 | 0.00275 | 0.06985 | 4 |
MT-11160 | 0.004 | 0.1016 | 6 |
Mould-Tech encompasses four series: A, B, C, and D. Among these, Mould-Tech Series A finishes are extensively employed in various products due to their wide range of fine to coarse matte finishes, eliminating the need for laser treatments, masked chemical etching, or other specialized texturing techniques.
For instance, MT-11010 exhibits a sand-like appearance, MT-11120 provides a smooth concrete look, MT-11555 presents a wood panel texture, and so forth.
Mould-Tech B
Serie Number | Texture Depth (Inch) | Texture Depth (Meter) | Draft Angle |
MT-11200 | 0.003 | 0.0762 | 4.5 |
MT-11205 | 0.0025 | 0.0635 | 4 |
MT-11210 | 0.0035 | 0.0889 | 5.5 |
MT-11215 | 0.0045 | 0.1143 | 6.5 |
MT-11220 | 0.005 | 0.127 | 7.5 |
MT-11225 | 0.0045 | 0.1143 | 6.5 |
MT-11230 | 0.0025 | 0.6350 | 4 |
MT-11235 | 0.004 | 0.1016 | 6 |
MT-11240 | 0.0015 | 0.0381 | 2.5 |
MT-11245 | 0.002 | 0.0508 | 3 |
MT-11250 | 0.0025 | 0.0635 | 4 |
MT-11255 | 0.002 | 0.0508 | 3 |
MT-11260 | 0.004 | 0.1016 | 6 |
MT-11265 | 0.005 | 0.127 | 7 |
MT-11270 | 0.004 | 0.1016 | 6 |
MT-11275 | 0.0035 | 0.0889 | 5 |
MT-11280 | 0.0055 | 0.1397 | 8 |

Mould Tech C
Serie Number | Texture Depth (Inch) | Texture Depth (Meter) | Draft Angle |
MT-11300 | 0.0025 | 0.0635 | 3.5 |
MT-11305 | 0.005 | 0.127 | 7.5 |
MT-11310 | 0.005 | 0.127 | 7.5 |
MT-11315 | 0.001 | 0.0245 | 1.5 |
MT-11320 | 0.0025 | 0.0635 | 4 |
MT-11325 | 0.003 | 0.0762 | 4.5 |
MT-11330 | 0.002 | 0.0508 | 3 |
MT-11335 | 0.002 | 0.0508 | 3 |
MT-11340 | 0.003 | 0.0762 | 4.5 |
MT-11345 | 0.003 | 0.0762 | 4.5 |
MT-11350 | 0.0035 | 0.0889 | 5.5 |
MT-11355 | 0.0025 | 0.0635 | 4 |
MT-11360 | 0.0035 | 0.0889 | 5.5 |
MT-11365 | 0.0045 | 0.1143 | 7 |
MT-11370 | 0.004 | 0.1016 | 6 |
MT-11375 | 0.004 | 0.1016 | 6 |
MT-11380 | 0.004 | 0.1016 | 6 |
Mould-Tech D
Serie Number | Texture Depth (Inch) | Texture Depth (Meter) | Draft Angle |
MT-11400 | 0.002 | 0.0508 | 3 |
MT-11405 | 0.0025 | 0.0635 | 4 |
MT-11410 | 0.0035 | 0.0889 | 5.5 |
MT-11415 | 0.002 | 0.0508 | 3 |
MT-11420 | 0.0025 | 0.0635 | 4 |
MT-11425 | 0.0035 | 0.0889 | 5.5 |
MT-11430 | 0.007 | 0.1778 | 10 |
MT-11435 | 0.01 | 0.254 | 15 |
MT-11440 | 0.0005 | 0.0127 | 1.5 |
MT-11445 | 0.0015 | 0.0381 | 2.5 |
MT-11450 | 0.0025 | 0.0635 | 4 |
MT-11455 | 0.003 | 0.0762 | 4.5 |
MT-11460 | 0.0035 | 0.0889 | 5.5 |
MT-11465 | 0.005 | 0.127 | 7.5 |
MT-11470 | 0.002 | 0.0508 | 3 |
MT-11475 | 0.002 | 0.0508 | 3 |
MT-11480 | 0.003 | 0.0762 | 4.5 |
Due to the coarser features of Mould-Tech surface textures compared to SPI finishes, a more aggressive draft angle is required during the moulding process. It is recommended to add 1.5° of draft for every 0.001″ of texture depth to ensure smooth and efficient demolding.
Mould-Tech surface textures provide a wide range of options for achieving desired aesthetic effects and functional characteristics in injection-moulded products. Manufacturers can select the appropriate Mould-Tech specification based on their design requirements and desired surface appearance.
And in case you are not familiar with Draft angle. The draft angle refers to the degree of taper applied to moulded or cast parts perpendicular to the parting line. It serves several purposes in injection moulding. Firstly, it reduces the risk of part damage caused by friction during release and minimizes wear and tear on the mould. Secondly, it ensures a uniform, smooth, and unscratched finish when desired, while also maintaining the integrity and consistency of other surface finishes and textures. Additionally, incorporating draft angles can decrease overall cooling time by eliminating the need for unconventional ejection setups. These benefits ultimately lead to cost reductions in production.
Draft angles are typically necessary in injection moulding design, with only a few exceptions for certain soft materials like nylon that can tolerate zero draft angles. Design for manufacture should include the consideration of draft angles from the outset, involving product designers, design engineers, and customers to address design requirements effectively. It is generally preferred to have some draft angle rather than none at all.
Types of Surface Textures: VDI Injection moulding surface finish
VDI surface finish refers to the mould texture standard established by the Society of German Engineers. This standard is widely adopted by tool producers globally, including in North America, Europe, and Asia. The VDI 3400 surface finish specification is primarily achieved through Electrical Discharge Machining (EDM) during the mould machining process. However, it can also be attained using traditional texturing techniques such as grit, stone, and sandpaper.
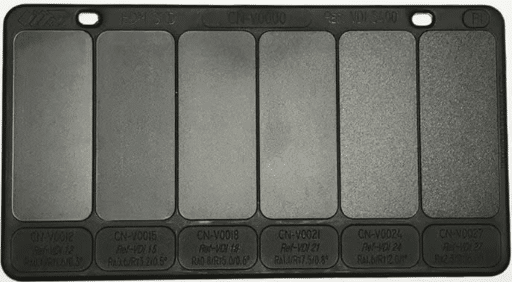
The VDI surface finish standard provides a comprehensive set of guidelines and classifications for specifying and achieving desired surface textures on injection-moulded products. It offers manufacturers a common language and reference point to communicate and achieve consistent surface finishes across different tooling processes and geographic regions.
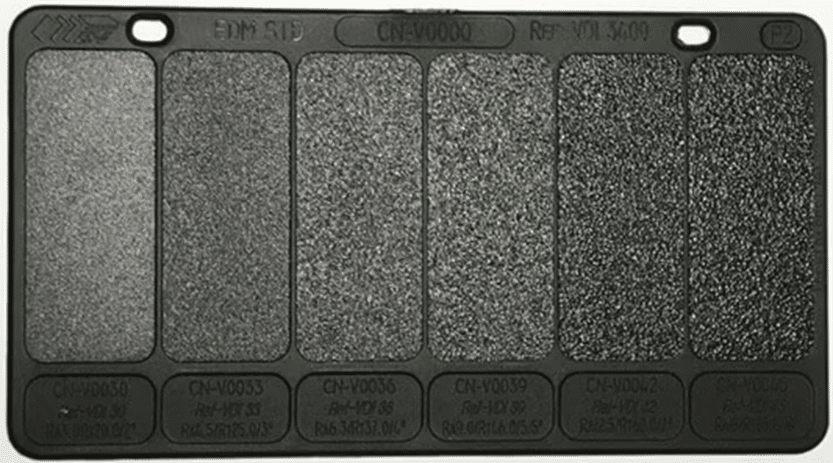
The VDI surface finish standard serves as a valuable resource for designers, engineers, and manufacturers in selecting the appropriate surface texture based on their specific requirements. It ensures consistency, quality, and performance across different moulding processes and enables the creation of visually appealing and functional injection-moulded products.
VDI Value | Description | Applications | Surface roughness (Ra) | |
µm | µinch | |||
12 | 600 Stone | Low polish parts | 0.4 | 16 |
15 | 400 Stone | Low polish parts | 0.56 | 22 |
18 | Dry Blast Glass Bead | Satin finish | 0.8 | 31 |
21 | Dry Blast # 240 Oxide | Dull finish | 1.12 | 44 |
24 | Dry Blast # 240 Oxide | Dull finish | 1.6 | 63 |
27 | Dry Blast # 240 Oxide | Dull finish | 2.24 | 88 |
30 | Dry Blast # 24 Oxide | Dull finish | 3.15 | 124 |
33 | Dry Blast # 24 Oxide | Dull finish | 4.5 | 177 |
36 | Dry Blast # 24 Oxide | Dull finish | 6.3 | 248 |
39 | Dry Blast # 24 Oxide | Dull finish | 9 | 354 |
42 | Dry Blast # 24 Oxide | Dull finish | 12.5 | 492 |
45 | Dry Blast # 24 Oxide | Dull finish | 18 | 709 |
Factors to Consider While Deciding Mould Surface Textures
Choosing the appropriate injection moulding surface finishes involves considering several factors, including part function, material selection, visual requirements, manufacturing constraints, cost analysis, and aesthetics. The selection of surface finishes should be determined during the early stages of the product design process, as it influences material selection, draft angles, and tooling costs.
Aesthetics and Functionality
- Injection moulding textures have the potential to enhance both the appearance and functionality of parts. The desired aesthetic value of the parts will guide the selection of the appropriate surface finish grade.
- For example, a smooth and glossy finish may be preferred for products with a high-end, visually appealing look, while a textured or matte finish may be suitable for industrial or functional parts that require improved grip or camouflage of imperfections.
Material Selection and Compatibility
- The selection of the mould surface texture should be influenced by the material used for injection moulding. Different materials possess distinct physical and chemical properties that can impact the surface finish.
- Factors such as melting temperature, flow characteristics, and shrinkage behaviour should be taken into account. Certain materials may lend themselves better to specific surface finishes, and understanding these material-texture interactions is crucial for achieving the desired outcome.
Injection Speed
- The injection speed of the molten material during the moulding process also plays a vital role in surface texture quality. A faster injection speed can result in a smoother and more glossy finish, as it allows the mould cavity to fill quickly and uniformly.
- The rapid filling minimizes the formation of imperfections and defects, resulting in a higher-quality appearance. On the other hand, slower injection speeds may be preferred for achieving specific textured or matte finishes that require more controlled material flow.
Manufacturing Constraints and Production Efficiency
- The Injection Moulding and production requirements can influence the choice of surface texture. Factors like tooling capabilities, mould complexity, and cycle time considerations should be evaluated.
- Certain surface finishes may require specific manufacturing techniques or equipment, and their feasibility and efficiency should be assessed in relation to the production process.
Cost Analysis and Budgetary Factors
- The cost implications associated with different surface finishes should be evaluated. Factors such as tooling cost, maintenance, surface treatment expenses, and overall production costs need to be considered.
- Higher-quality surface finishes or specialized texturing processes may incur additional expenses, which should be balanced against the desired outcome and project budget.
Customer Preferences
- The visual appearance and customer expectations are important factors in surface finish selection. The desired level of glossiness, texture, pattern, or special effects should align with the intended aesthetics and brand image of the product.
- Consumer preferences and market trends should also be taken into account to ensure the final product meets or exceeds customer expectations.
Conclusion
The selection of surface textures in injection moulding is a crucial consideration that significantly influences the overall performance, visual appeal, and quality of the final product. Surface textures influence the functionality and performance of the part, including grip, wear resistance, and friction. They enhance the visual appeal and aesthetics of the product, aligning with customer expectations and market trends. Surface textures can help hide machining marks, imperfections, or deformations on the part’s surface. Different materials and applications may require specific surface finishes for optimal performance and compatibility.
Choosing the right surface texture for injection moulding requires careful consideration of design requirements, material compatibility, manufacturing constraints, cost analysis, and aesthetic preferences. Collaborating with experienced mould designers, toolmakers, and surface finishing experts is crucial to ensure the desired outcome and the successful realization of the product.
As technology advances, new surface texturing techniques and standards may emerge, offering even more possibilities for achieving desired surface finishes. Staying updated with the latest industry developments and leveraging advancements in moulding technologies can help manufacturers enhance their product quality, customer satisfaction, and competitiveness.